Western Container Corporation (WCC) was founded by a group of independent bottlers of The Coca-Cola Company (TCCC)in 1979. What motivated them?
Eric Scott: Two factors were paramount: the location of the Coca-Cola bottlers in West Texas made bottle supply logistics difficult and unpredictable, and bottle transportation costs were cost prohibitive. In 1979, most of the bottles filled were 2-litre, and a truckload carried only 28,000 containers, resulting in excessive costs considering the distances involved. With the formation of Western Container, both problems were solved.
Nearly 40 years have passed and WCC has grown to one of the largest PET convertors in the USA. What does the company look like today?
Eric Scott: Western currently produces approx. 6.5 billion preforms and nearly 3 billion bottles per year. In other words, we sell more preforms than bottles, which wasn’t always the case. Our annual sales come to about USD 320 million, influenced heavily by the price we pay for PET resin. Our customers are our shareholder owners and they consist of five very large and a few smaller bottlers. We supply a total of 40 bottler locations from our four production facilities in Fife, Hattiesburg, Houston and Tolleson, and with our Sugar Land, TX headquarters employ approx. 330 people.
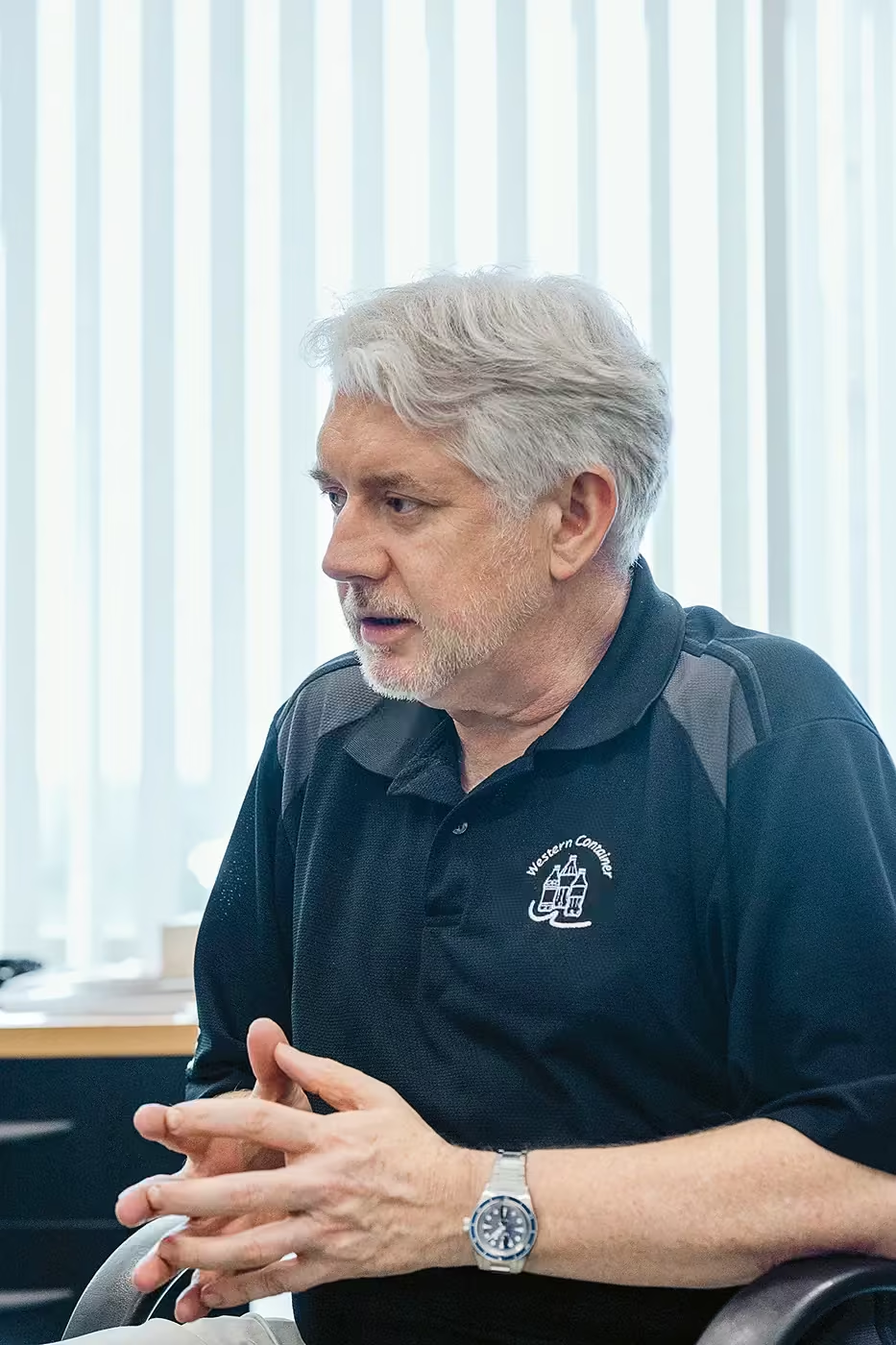
Your customers are bottlers for Coca-Cola exclusively. What is your biggest challenge?
Eric Scott: Over the years we’ve been able to implement a very simple mission statement. It consists of guaranteeing our preforms and bottles are the highest quality, with surety of supply, and at the lowest possible cost. Since profit is not our first objective, we continue to focus on cost reduction, and we believe we’re quite good at it. In the 14 years that I’ve been with the company, we’ve reduced our production costs each year, and this despite steadily increasing costs of labour, energy and raw materials. At the same time, we have seen dramatic improvement in our quality metrics.
What does it look like as regards energy?
Roger Kerr: Approximately 16 years ago, we started measuring our energy consumption and subsequently have reduced the energy to produce our preforms and bottles on an annual basis. We recorded significant decreases in the early years, but in the last five years or so, we have aimed at a two-percent reduction annually, which we usually meet or surpass. Thanks to the daily efforts of our corporate and production teams, we now use approximately 40 per cent less energy than when we started measuring in 2003. In addition to this, we carefully look at energy consumption when investing in new equipment. Technologies are now in the market that weren’t previously available, for example Kinetic Energy Recovery Systems, which have been popularised in Formula One racing are now available in injection moulding systems. These and other energy-saving technologies are now making real tangible improvements, providing both financial savings and lowering our carbon footprint.
Where do you see potential for further cost reductions?
Eric Scott: Automation and telemetry continue to advance at an ever more rapid pace – both in general and within our industry. We currently have two big projects under way. In Hattiesburg, we are installing a fully automated preform warehouse system due to start up this year. This system utilises laser-guided vehicles (LGVs) to collect preform bins from our injection department and store them in our preform warehouse. The LGVs subsequently fetch the bins for loading onto trucks. This is truly an autonomous “lights-out” operation, which will be monitored from our production control centre. We expect this system to increase our handling efficiency, reduce costs, improve safety and give us real time inventory data.
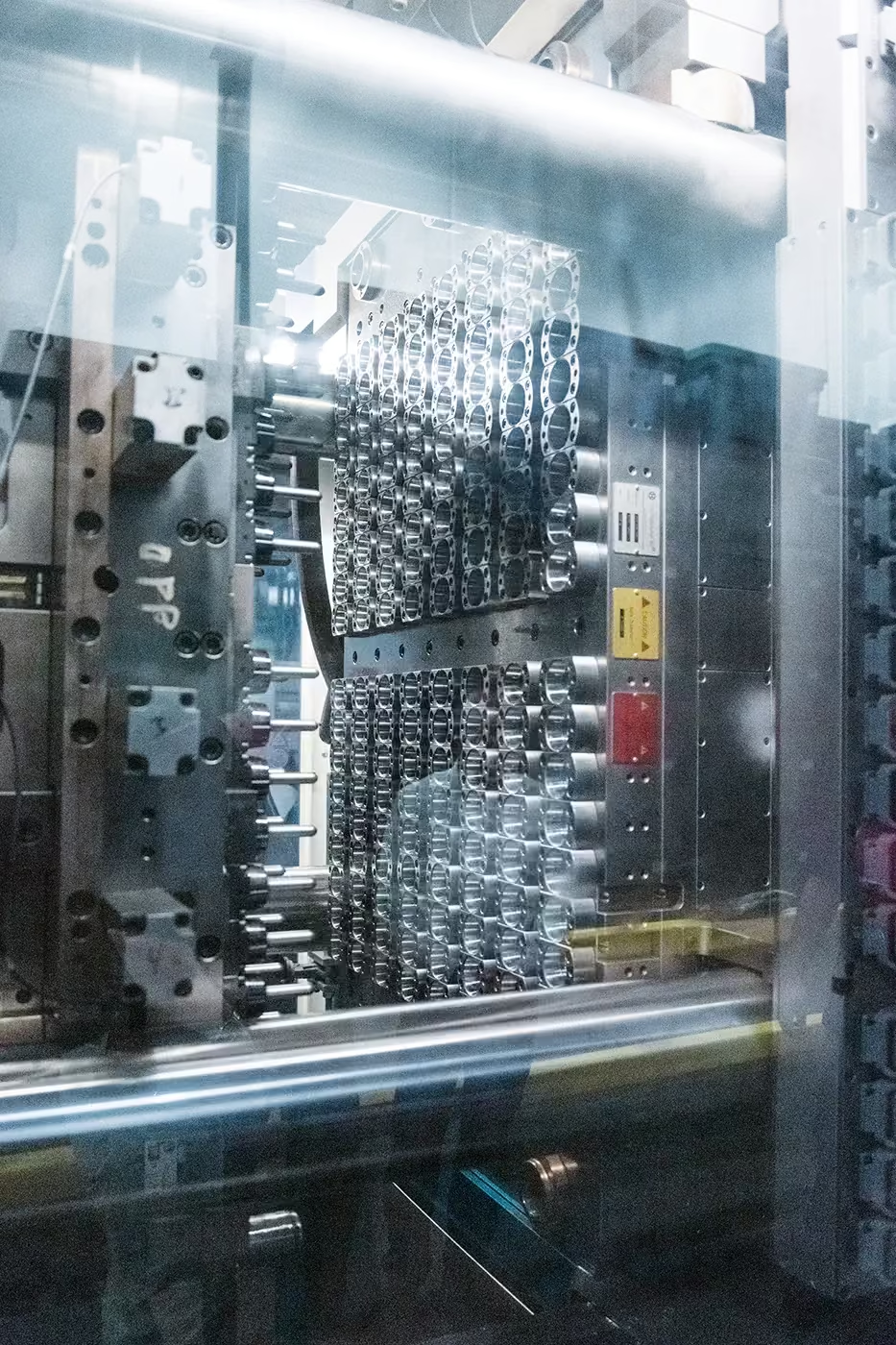
Also, in Hattiesburg, we continue to refine our newly installed production control centre that allows us to monitor critical indicators in our injection, water, air, power and resin systems. This is truly process control: we no longer check part quality exclusively, but monitor real-time-critical indicators, ensuring we build quality into our products. Our production teams no longer spend hours inspecting individual parts; they devote their time to looking for process variables which are trending away from their setpoints, giving us time to take corrective action before it becomes an issue. This dovetails into one of my major company themes, “Every role adds Value”, and it is critical to our success.
Will it also be possible to monitor other plants from the same control room?
Roger Kerr: Absolutely. With today’s technology everything can be monitored remotely. With our control room concept, we are taking our first steps in this direction. In the coming months, Hattiesburg will monitor the injection systems at Houston. The Hattiesburg team have a very deep understanding of injection systems, and also have more resources than their colleagues in Houston. This makes them ideal for helping Houston undertake process monitoring, while still enabling us to run as lean as possible with only four injection systems located there.
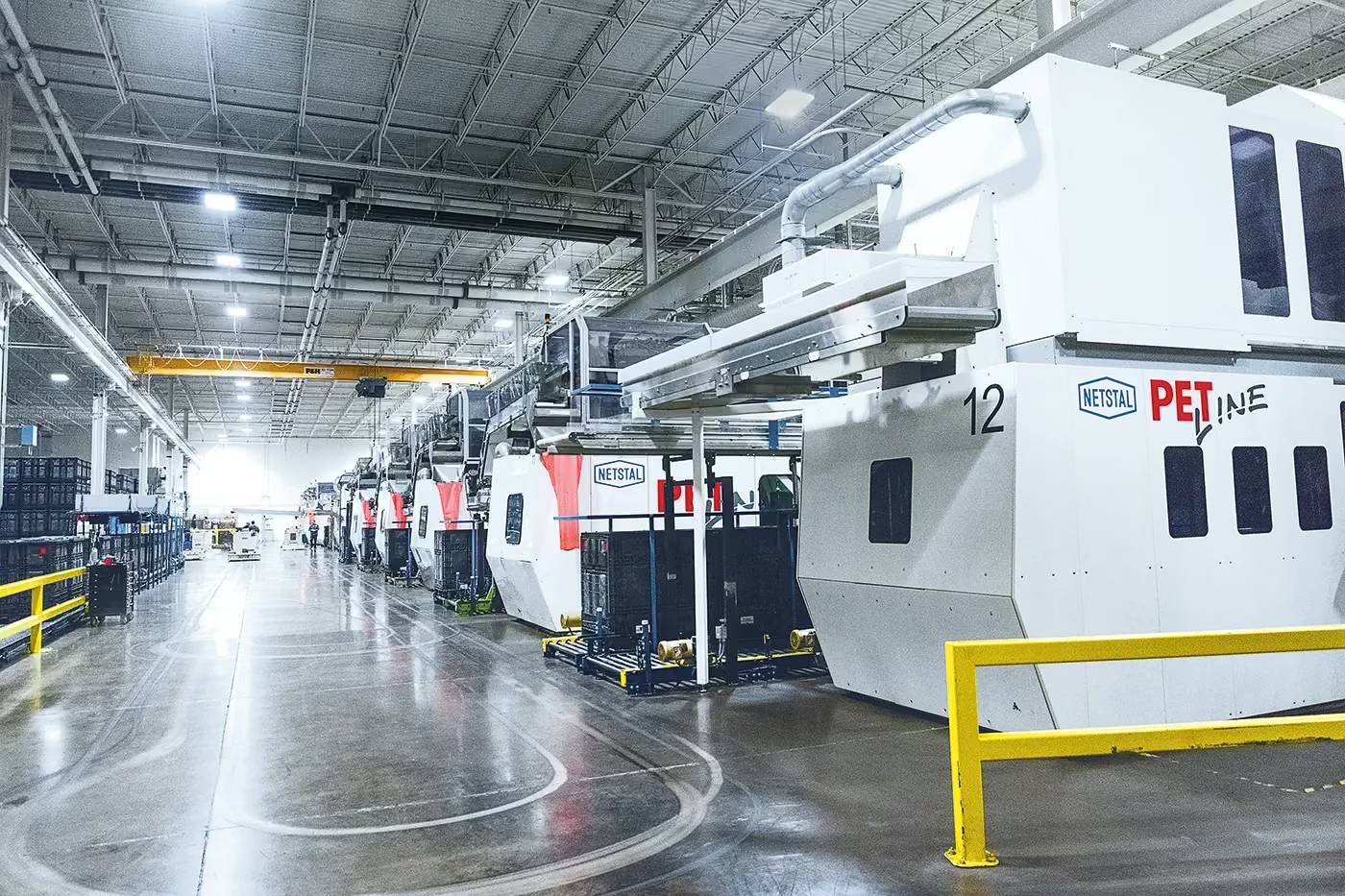
To what extent will these developments affect the work of your employees?
Eric Scott: Shifting focus from “Quality by checking” to “Quality by process monitoring” is very important to us at Western Container. We want all roles to add value, and this is a big step in that direction. To monitor the process of a complete production site is far more valuable than visual inspection alone. We shall either automate or adapt every activity until it creates direct additional value for the product or the process. In my view, this aspect makes us stand out in our branch of the industry.
Your mission is to supply your customers with the highest quality at the best price. How do you define highest quality?
Roger Kerr: We are not in the business of manufacturing the perfect preform or bottle. We define highest quality as parts that are both fit for purpose, run seamlessly through our bottlers’ equipment, and meet all TCCC standards. We mustn’t forget that no one wants to pay for perfect parts, but on the other hand, we try our utmost to keep potential issues from reaching our customers. We strive to do this by ensuring all our equipment is impeccably maintained, and ask our bottling partners to rate our quality performance on a regular basis.
How do you guarantee quality across all four plants?
Eric Scott: Faith Vedder is our Corporate Director of Quality and she has devoted herself to the pursuit of excellence for more than 30 years, developing numerous PET packaging quality systems for TCCC. All four plants operate the same quality system with a Quality Manager in each operation, ensuring all quality systems are complied with. We also have a corporate TCCC-certified laboratory, where preforms and bottles from both our and our bottlers’ facilities are regularly tested.
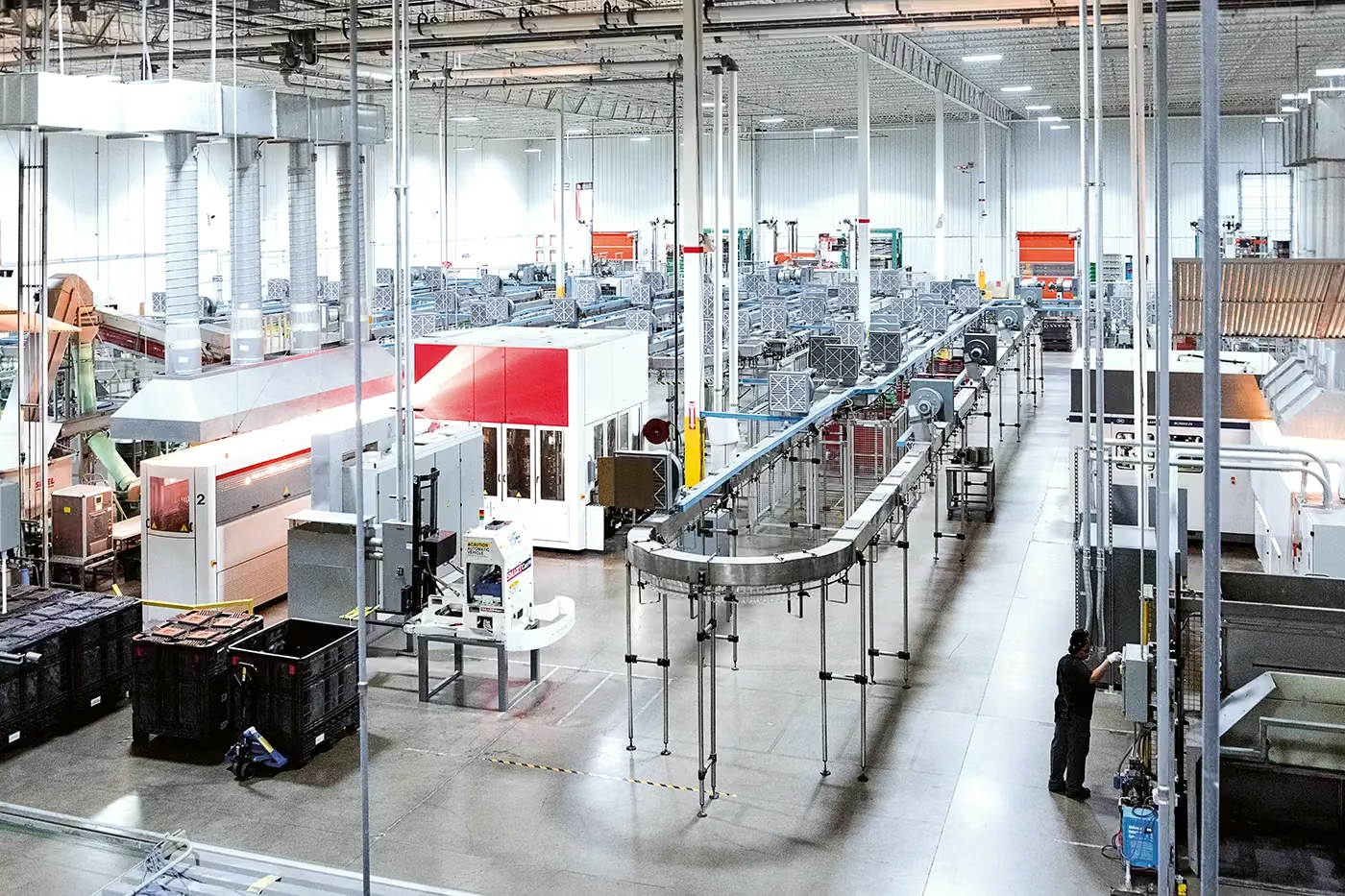
Earlier on you mentioned the importance of your equipment. What are your experiences with the injection moulds of Otto Hofstetter AG?
Roger Kerr: We haven’t lost a single cavity in the two years in which we’ve been running moulds from Otto Hofstetter AG (OHAG). This alone is testament to the workmanship we’ve come to expect from OHAG. Add to this the exceptional longevity of the tooling, which we independently verified with other OHAG users in the TCCC system, and you have a winning combination. OHAG has a unique cavity lock mould design, giving much better life than traditional stack designs. We fully expect to get 10 million plus cycles, possibly more, from our OHAG tooling before needing refurbishment. Our flash reports indicate we are right on track to exceed this target.
Eric Scott: I would like to add another point. Mould maintenance influences the economic efficiency of a system more than the energy effort. Therefore, if the life of a mould can be doubled, the costs for its maintenance are halved. In other words, the moulds of Otto Hofstetter AG help us to offer the highest quality at the best prices.
What could be optimised on the moulds of OHAG?
Roger Kerr: Although we are delighted with our OHAG moulds, no one can stand still, and we are pleased to see that OHAG is constantly striving for improvements. For the future I believe there are further cycle improvements that can be made through optimising the material flow paths in the hotrunner. We have seen first-hand that composite melt flow channels that have smooth flow paths improve melt flow while allowing reduced temperatures allowing shorter cycle times. More efficient mould venting is also another potential area for cycle time optimisation.
What about the available services?
Roger Kerr: It would be great if OHAG had a technician based in the USA, but we understand this is not an economical proposition until the user base expands. What we really need in case of a serious problem, however, is a solution within 24 hours, which OHAG already guarantees. Our technicians have also received excellent training in Switzerland, allowing us to cope with any issues that have arisen.
The first mould of Otto Hofstetter AG was put into production at your plant in 2001. The second one followed 15 years later. What did the Swiss do wrong in the meantime?
Roger Kerr: Nothing. About a year after receiving our first 96-cavity OHAG mould, we changed our 20-oz preform design, and another mould-maker offered us a 144-cavity mould for a Netstal system, which OHAG wasn’t offering at that time. Later Netstal offered us a 192-cavity system and unfortunately our relationship with OHAG took a back seat. The first Netstal-OHAG system was our fastest 20-oz system at the time, but its output could not match the later, larger cavitation moulds. Luckily, for me our relationship with OHAG was re-kindled when Netstal introduced their new 5000 system. At that time, Eric and I visited OHAG’s manufacturing plant in Uznach and were very impressed. We also visited a large user of OHAG moulds in Germany, who had very good things to say about the quality and longevity of the Swiss moulds, and at that point we were sold, and purchased our first Netstal 5000 with an OHAG 144-cavity mould. We have since bought another three Netstal 5000s with 144-cavity OHAG moulds.
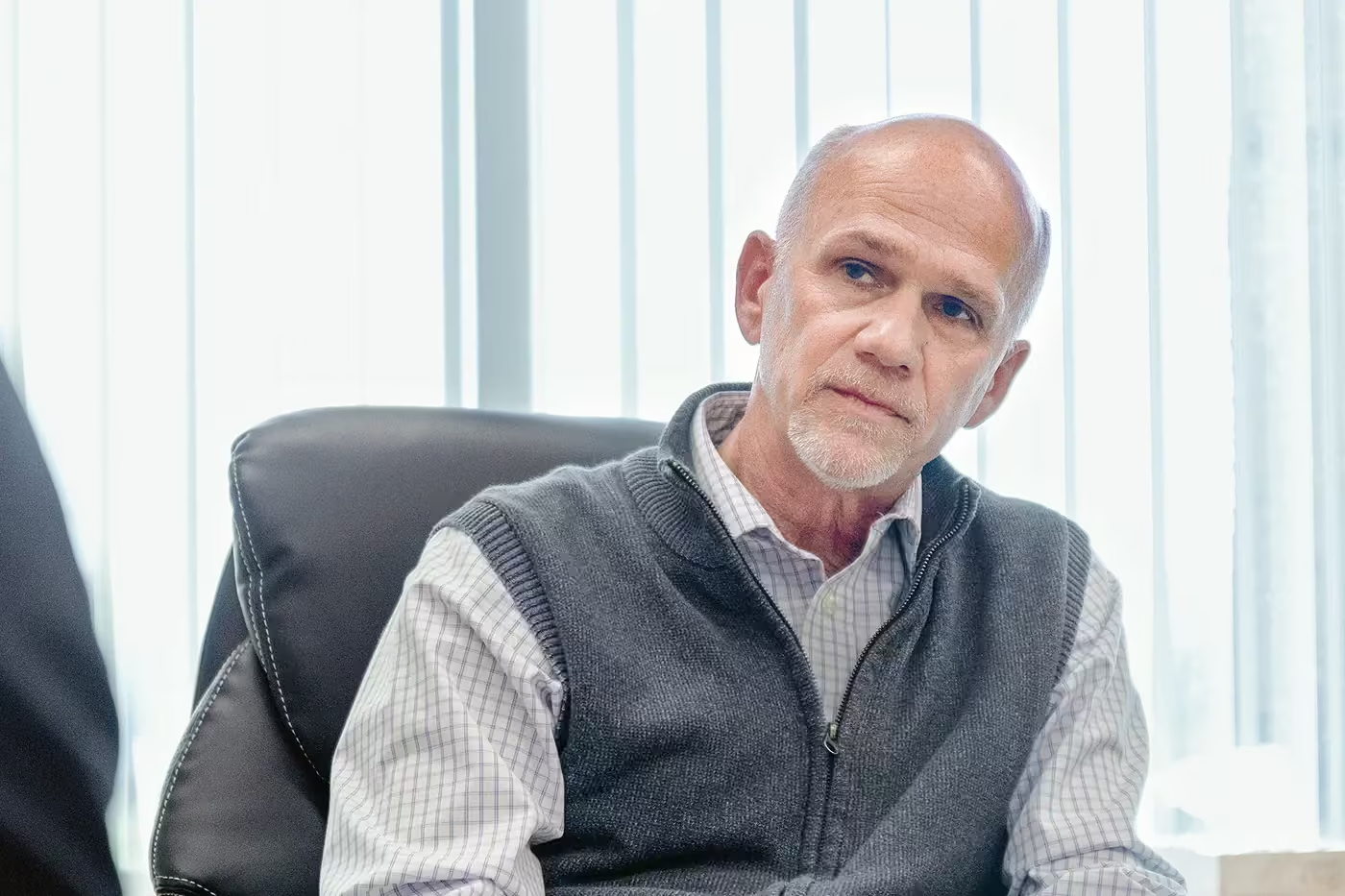
TCCC was one of the first global brands using recycled material. In what direction will the market develop as regards raw material?
Eric Scott: TCCC has announced a programme “World without waste”. Post-consumer recycled (PCR) granulate plays an important role in this. While I welcome this devel-opment, I also understand Roger’s concerns from a technical point of view. The biggest challenge is probably to get the necessary quantity of recycled material to supply a large convertor like ourselves. The consumers in the USA are not good recyclers yet, and as far as I know, the return rate is currently at approx. 30 per cent. Currently this recycled resin is used in multiple ways, not just for bottle production. We will only get enough raw material if the beverage producers, bottle-makers, consumers and the State cooperate.
Roger Kerr: We currently produce Dasani PET water bottles with PlantBottle resin formulated with 30 % ethylene glycol from sustainable sources. This has been a major initiative of the TCCC and has demonstrated their will-ingness to tackle some of the big environmental challenges.
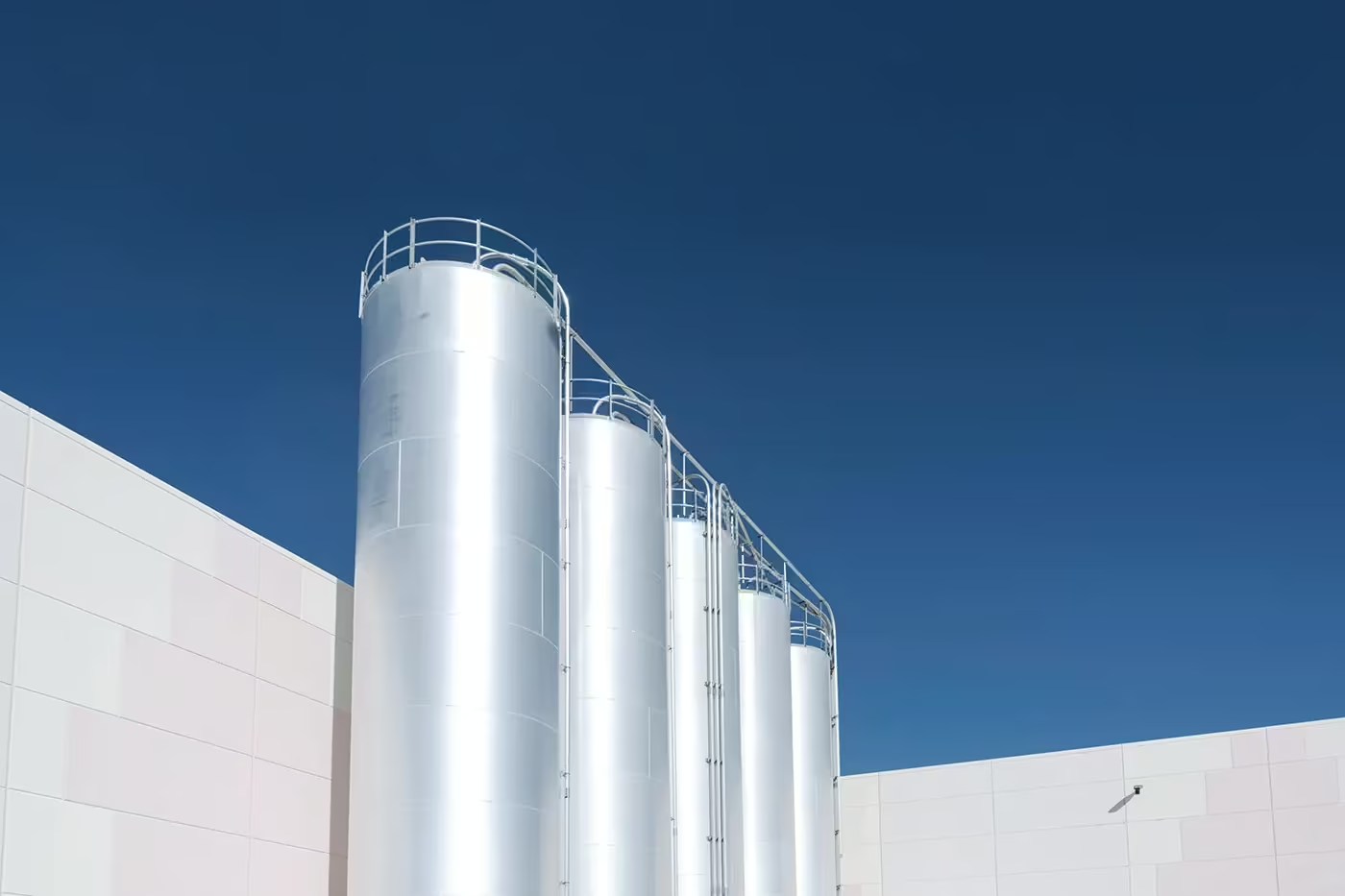
What will Western Container look like in five years from now?
Eric Scott: We will probably see further in-line blow systems in operation. At Western Container we are concentrating on the production of preforms, and we will continue to serve our bottlers in any way that adds value. Thanks to automation, in the future we aim to produce more, with fewer employees, while offering them tasks that are more rewarding.
Roger Kerr: With the moulds of Otto Hofstetter AG running on Netstal 5000 moulding systems, we already produce over 1.6 billion preforms per annum. A number hardly anybody believed possible only a few years ago. I’m confident that as our systems continue to be developed, we shall produce more preforms with much fewer machines.
Eric Scott: We are blessed to have the backing of our bottlers under the Coca-Cola umbrella, and I am confident that with the right people, and the right technology, Western has a very bright future.
Many thanks for the discussion and best wishes for your continued success.
- Sugar Land (company domicile), Fife, Hattiesburg, Houston and Tolleson (plants)
- Founded in 1979
- Employees: 330 persons in total
- Range of products: preforms and bottles for fillers of The Coca-Cola Company in the USA
- Capacity: 6.5 billion preforms, 3 billion bottles