What, in brief, is the history of HAITAI HTB Co., LTD?
Our company was originally a subsidiary of the Haitai Confectionery & Foods Company, which was founded in 1945, i.e. before the country was divided into South and North Korea. The enterprise expanded its business activities in different directions. By 1997, the entire Haitai Group comprised 15 sister companies. In the year 2000, HAITAI HTB Co., LTD –abbreviated HTB – withdrew from the group and was taken over a year later by LG Household & Health Care Ltd.
How is the enterprise structured today?
LG Household & Health Care Ltd. was created as a spin-off of LG Chemical, Ltd. in 2001 and has developed steadily ever since. At present, the company consists of three divisions operating under the keywords “beautiful”, “healthy” and “refreshing”. The complete beverage business is part of the third and consists in turn of five areas, among them Coca-Cola, fruit juices and mineral waters.
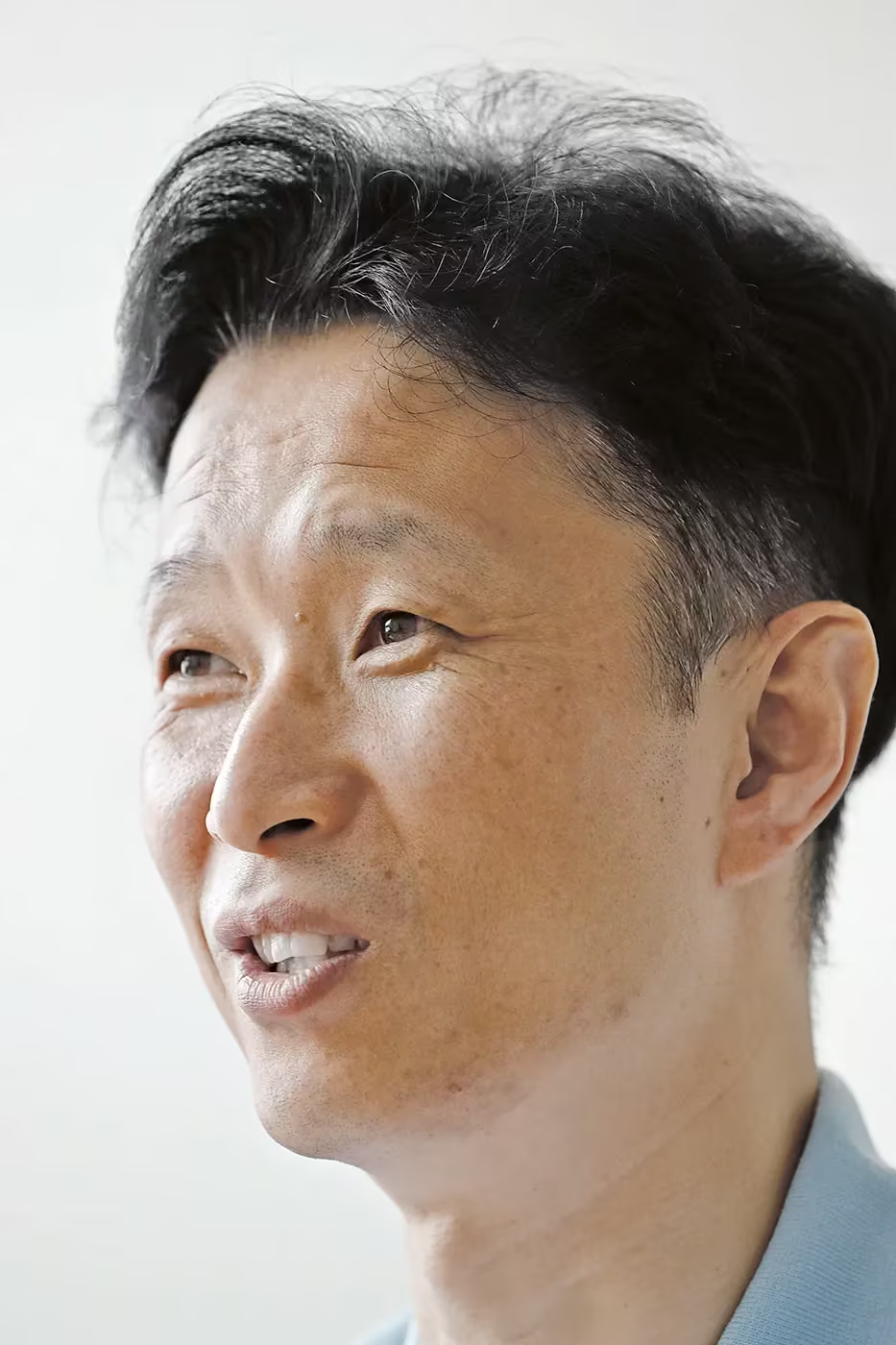
How is HAITAI HTB Co., LTD set up?
Our company was founded in 1973 and ranks among South Korea’s leading beverage producers. Apart from the Pyeongchang factory, located 130 kilometres to the east of the capital Seoul, we operate two further locations. HTB was the first company to launch many different juice beverages, including carbonated types, on the South Korean market.
In 2011, we acquired the water producer Diamond Pure Water, which was founded in 1972. This merger allowed us to strengthen our position in the water market.
What are HTB’s most important products?
Of high importance are our natural fruit juices, juice drinks –with and without fizz – sports drinks as well as traditional Korean beverages such as fermented rice drinks and Chinese drinks. Our second important pillar is natural mineral water, as was already mentioned. Moreover, HTB has been a licensee of the Californian Sunkist Growers Inc. for the South Korean market since 1976.
What kind of capacities are we talking about?
Within HTB we have two factories in which we produce water, in total roughly 200,000 metric tonnes or 200 million bottles per year. Apart from this, we mould preforms for Coca-Cola in South Korea. For this latter segment we make a capacity of 200 million more bottles available.
These are impressive figures. What infrastructure allows you to achieve this output?
We run three lines to produce the 400 million preforms annually. The “motor” of each production line is a Netstal PET-Line 4000 injection moulding machine. We differentiate as regards the injection moulds. Four of these moulds feature 96 cavities each, and one has 128 cavities.
What are your main markets and how are they split up?
We produce mainly for the domestic market. Only about five per cent of the juice drinks are exported. In other words, our products are above all found in shops in South Korea. And they are popular. The Pyeongchang Drinking Water has been able to gain an additional five per cent of market share.
How big is the water market in South Korea?
The current market value is approximately USD 600 million and grows by about 15.5 per cent annually. The reasons for this are the growing number of single-person households and the health trend. According to forecasts the water market will grow to a total value of USD 900 million by 2020.
What is HTB’s position in the South Korean beverages market?
Together with Coca-Cola we are number one in Korea for beverages. In the juice drinks segment we take second place and in the area of mineral water we fight with other producers over the positions. It changes from year to year. Normally, HTB ranks third or fourth.
What are the strengths of HTB in your view?
We’re proud of our outstanding quality. After that, we are proud of our cleanliness and excellent operational organisation. In the past we obtained the preforms from external sources, which required permanent and elaborate quality control. Everything is much more relaxed now that we prod-uce ourselves.
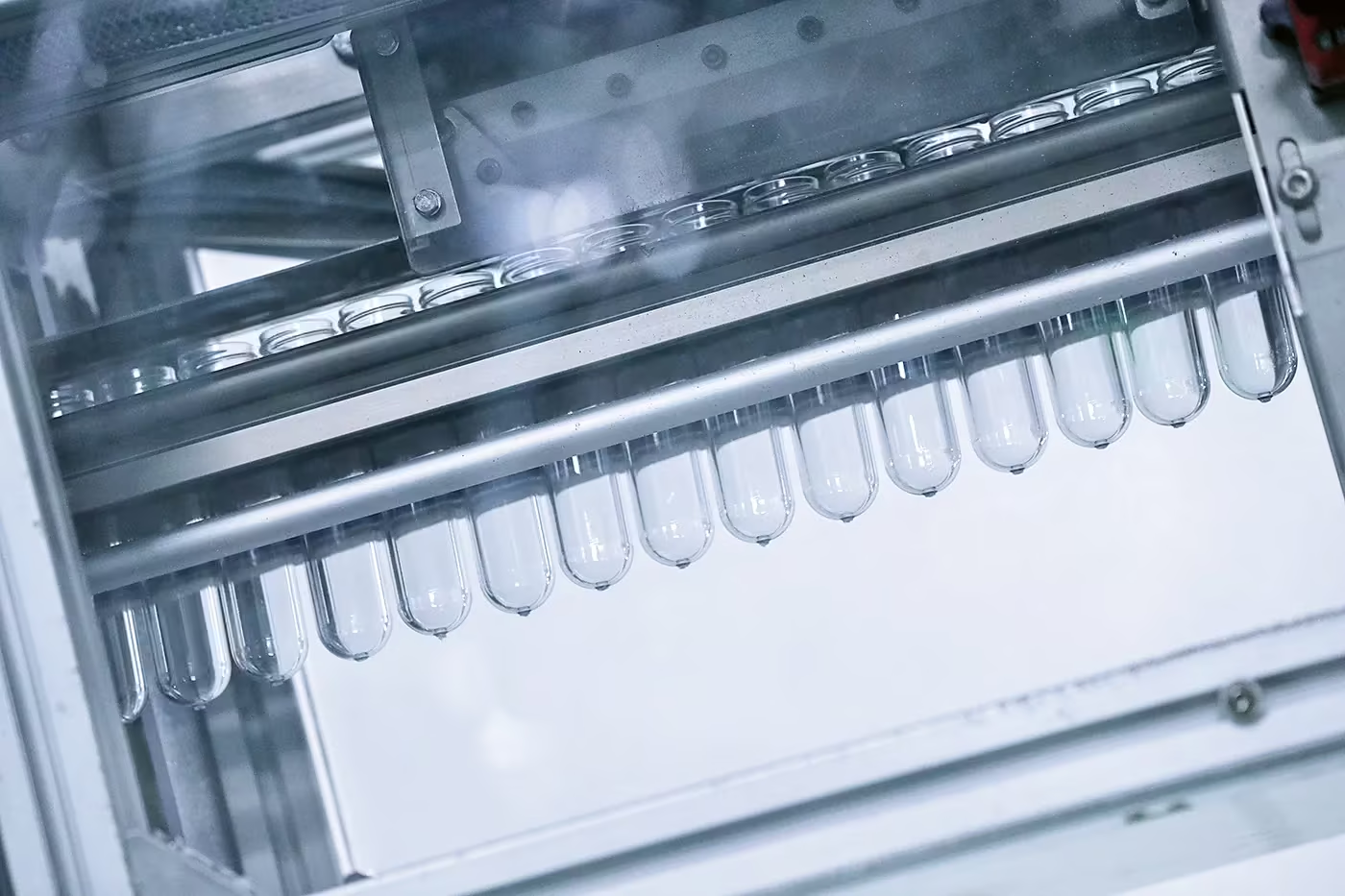
What were the most important tasks in the starting phase?
First of all we had to achieve the desired quality level. Prod-uctivity, costs and maintenance were other aspects which kept us busy at the outset. Now that these issues are settled, we devote ourselves to improving our technology.
What are the biggest challenges in the immediate future?
Future priorities are first-class maintenance and the ability to hold and expand our productivity. This at a consistently high level of quality, of course. We will further improve, reduce downtimes and guarantee gapless upkeep. The market as a whole keeps growing, i.e. demand increases automatically. We provide room for a further production system, if necessary by buying more land.
To what extent is sustainability a topic for HTB?
Pyeongchang Drinking Water is a purely natural product. It comes from a region which we call the Alps of Korea, a spring located 680 metres deep in a mountain. At HTB the water is processed in a closed system to ensure that the natural taste is preserved. Our focus is always on the quality of the product; the cost is secondary. This is what I call lasting.
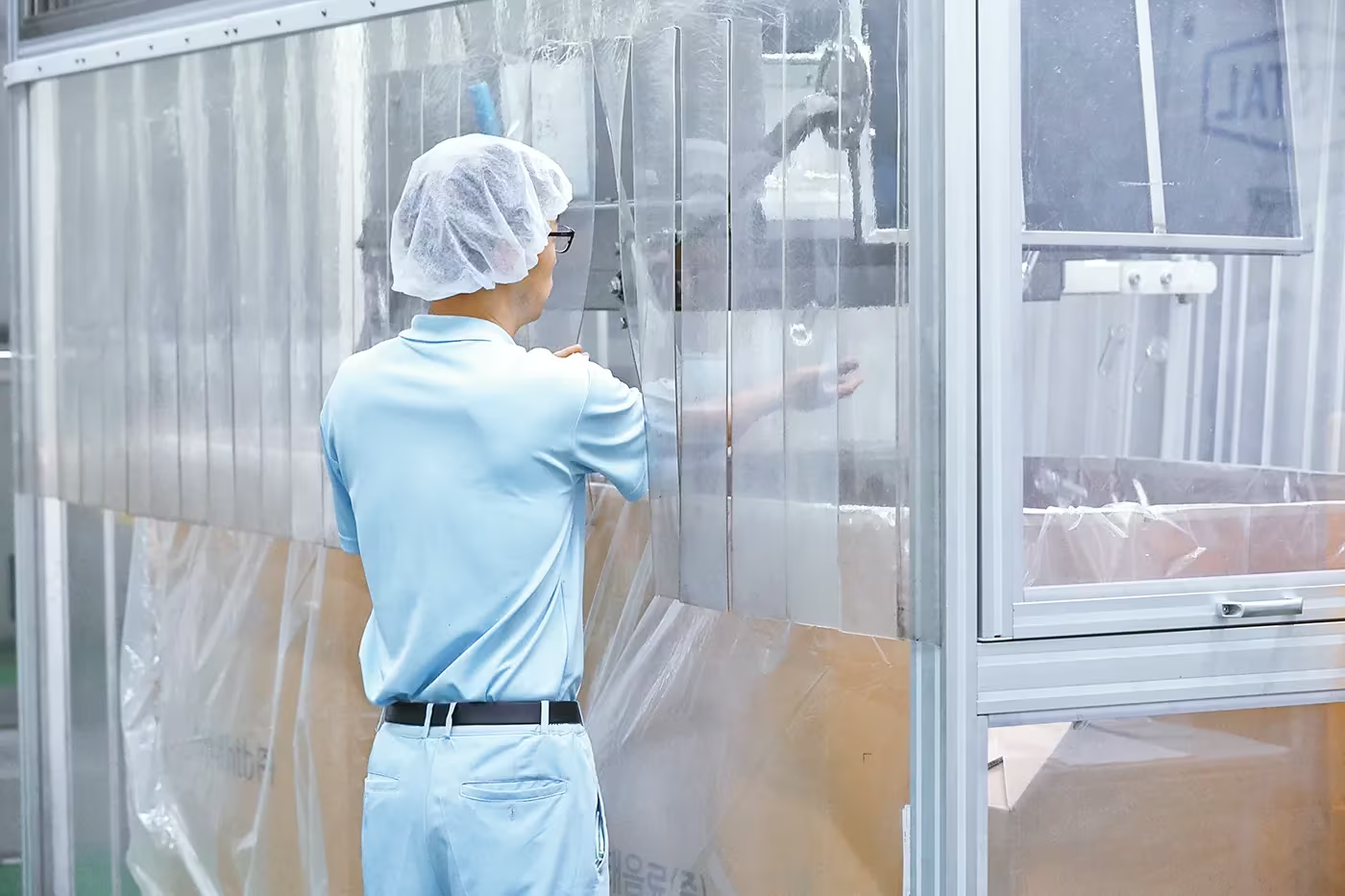
Nestlé and Danone have resolved to replace PET bottles with more environment-friendly packaging materials. Is this also a topic at HTB?
In South Korea, the trend towards environment-friendly products is hardly developed yet. Only a few and very reluctant approaches can be observed in this respect, mostly in the mineral water industry.
Where do you see potential for further market developments?
Certainly in the quality, for one thing. Apart from this, there will be new external possibilities. Next winter the Olympic Winter Games will be held here in Pyeongchang. The centre is only five minutes from our company. We have succeeded in becoming the official water supplier. This results not least in interesting advertising opportunities.
Since 2014 you have been relying on the quality of the preform moulds of Otto Hofstetter AG. What speaks in favour of these moulds?
Attaching top importance to quality and short downtimes, we looked for the most reliable moulds on the market. We chose Otto Hofstetter AG. Their moulds are simple and unique.
Where do you see possibilities for further optimising the moulds?
A better interchangeability of individual components would be very useful, but I was informed that work on this is already in progress. Another topic is the price, of course. Not only of the moulds, but also the fast reaction on the service side. These aspects will influence the decision as soon as the next investment is due.
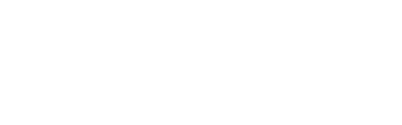