Five years have passed since I last interviewed an Italian producer of PET preforms. How has the market developed in the meantime?
The market situation in Italy has not changed very much in the last few years in terms of numbers. The branch of soft drinks, particularly mineral water, has seen a significant decrease in the weight of bottles and consequently of preforms. As a consequence, this situation has clearly produced important variations regarding the different types of neck finish, which has forced us to invest in moulds.
Where do you see the biggest challenges right now?
Since, as everybody knows, the price of raw materials (PET polymer) has been continuously fluctuating, it hasn’t been easy to face a very aggressive market. We understood that we had to lower our costs of production to meet the competition and be successful, so it was necessary to adapt our plants to the use of recycled polymers, fulfilling both the new European rules and the need to rapidly satisfy the requirements of our customers.
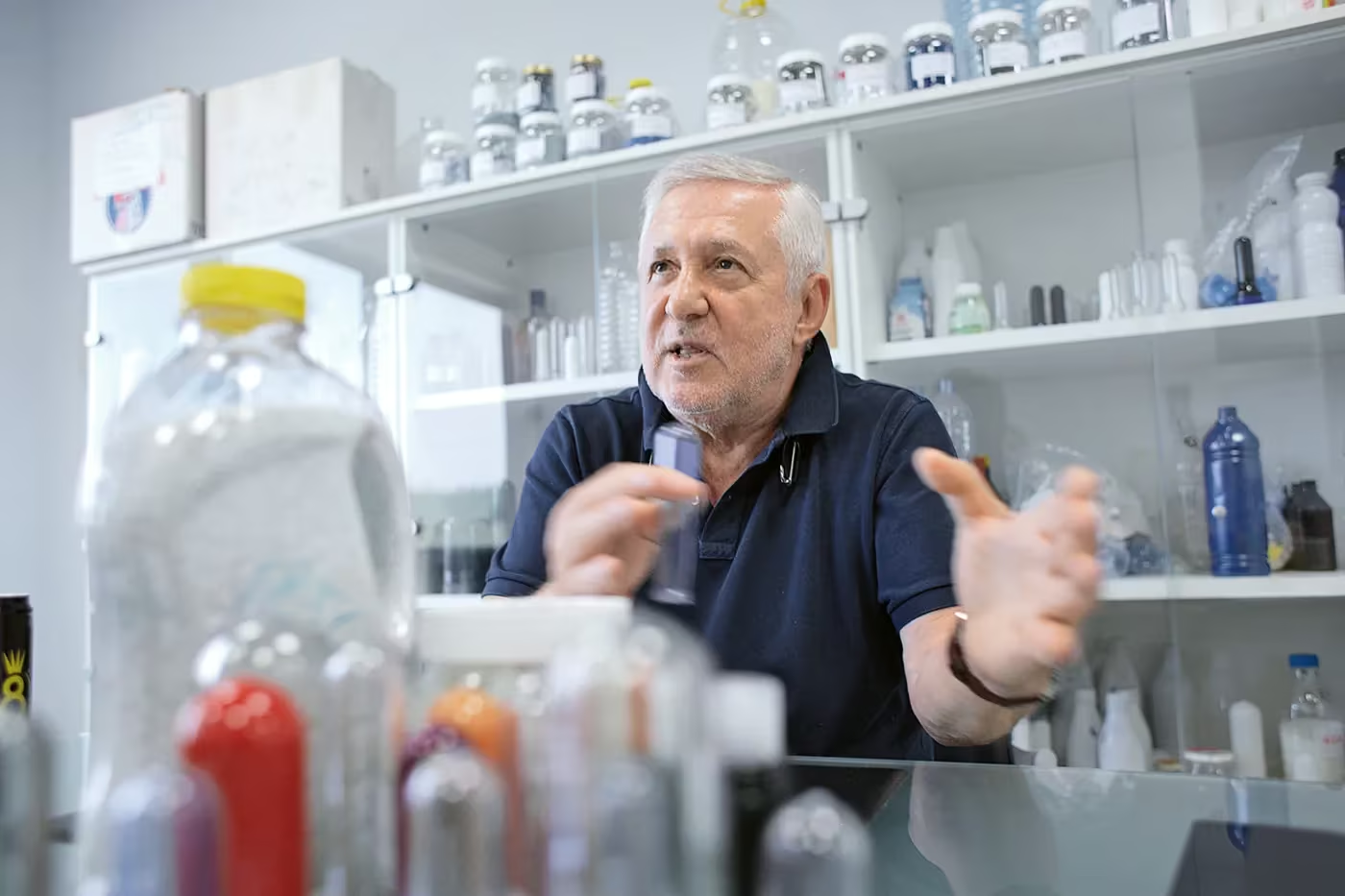
On your website, you refer to ongoing developments as regards both technology and quality. How do you ensure these developments?
We have always aimed to ensure efficiency, high-quality production and just-in-time service. And, in order to be able to do so, we made investments in a second trigeneration plant (the first one was opened 14 years ago), LGV internal transport, automated warehouses for the storage of products, and an automatic program to forward goods.
To improve quality, we have also installed online control systems and of course duly trained the staff in charge. All this now enables us to be very fast to react and satisfy any need.
You started at the company in 1997. What does it look like today?
Nuovaplast was born out of a company created in 1990 that was closed because of bankruptcy in 1996. There were only three lines of production then, and their capacity was of about 20 million preforms per month. In 1997, I received the proposal to manage and reorganise this company. My previous experience (from 1996) was in the direction and production of companies belonging to the branch of textile synthetics, mainly in the polyester field.
As a matter of fact, the raw materials used for both polyester production and PET preforms are the same, with the exception of polymer viscosity. After 22 years of hard work, Nuovaplast is now a well-known company in the Italian preform market and has now reached a production capacity of 2.5 billion preforms, with 14 production lines and a yearly use of 60,000 tonnes of PET polymer.
Our market is mainly formed by bottles for soft drinks and mineral water, which make up 70 per cent of the market, and bottles either for oil and milk or non-food items such as body care and cosmetic products and detergents, which make up the remaining 30 per cent.
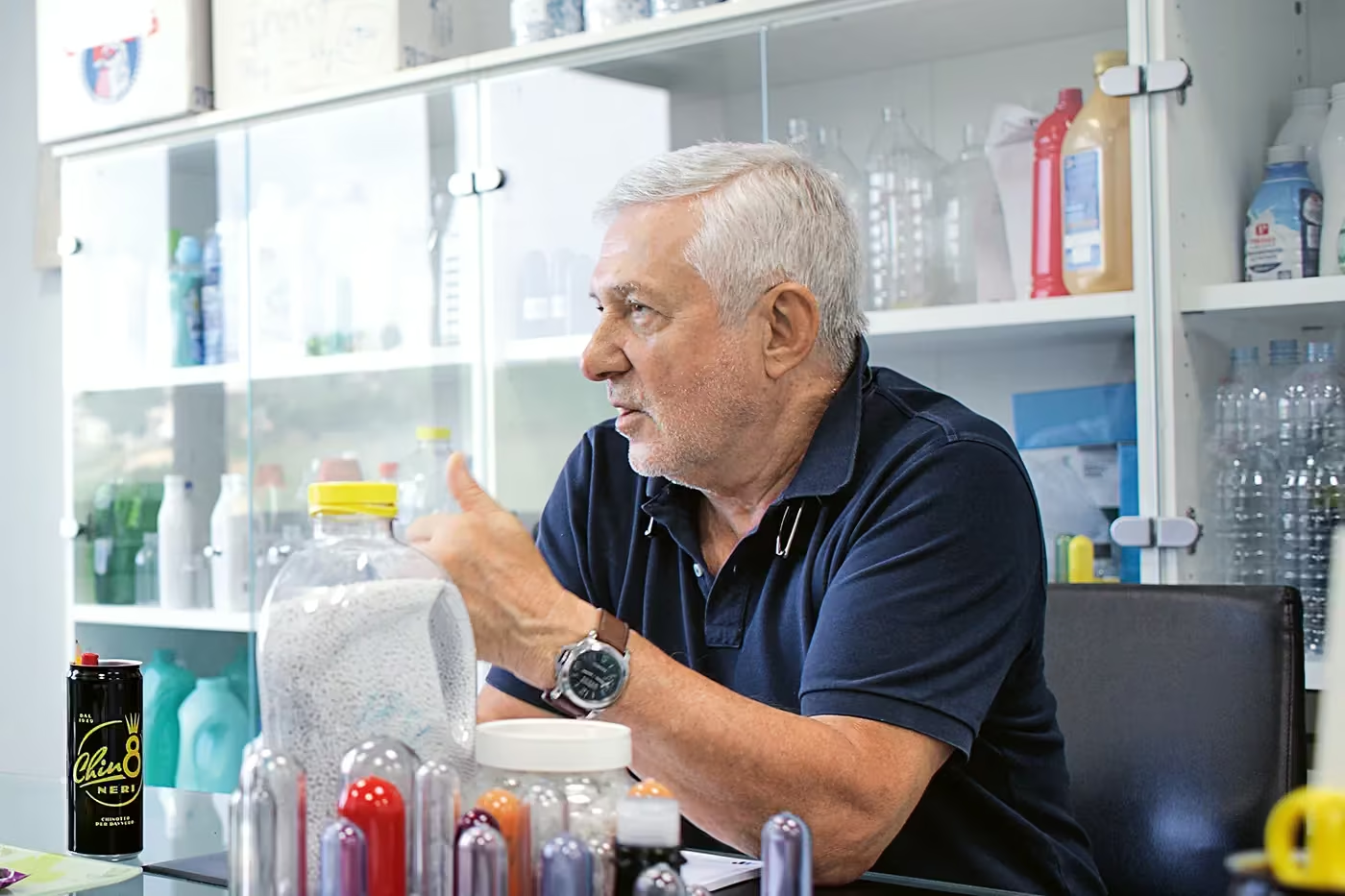
How is mould maintenance organised?
First, I must say that the quality of our production is a fundamental aim for all of us, so you can understand the reason why we place so much focus and importance on the care and maintenance of our plants, moulds and machines. The task of 20 per cent of our staff (50 employees) is the preparation and maintenance of our moulds.
Despite this, we would also like to increase this care, further favouring more collaboration with our suppliers and planning periodical checks and controls of our machines and moulds. This will undoubtedly allow us to react more quickly when required.
Co-injection is widely used for milk bottles, but not available from you. What is the reason for this?
The milk bottle industry is not our main field, but of course we know very well what the needs and developments in this particular market are. However, it is not yet very clear what effect multilayer preforms may have upon PET recycling. We are afraid that this technology may be rather paralysing as far as recycling and the use of pigments (TiO2) are concerned.
PET preforms are highly standardised. Why do your customers buy from you and not from a competitor?
Italy is a very unique country; nothing is really standard. Every producer tries to develop their products with features that must be different from their competitors. Nuovaplast has developed a high level of flexibility in its preforms so as to be able to satisfy the needs and specific requests of our customers. All this requires a lot of work and, together with good quality, excellent service and the right cost of production, allows us to stay ahead of the competition.
Villa Lempa is not very centrally located. What speaks in favour of this place?
The geographical position of our production site in central Italy allows us to take delivery of raw materials at a port (Ancona) which is quite close to us (170 kilometres). Secondly, we are situated rather close to our customers, enabling us to provide a prompt service for them, since they are mainly situated in southern Italy, where the production of mineral water is really very important.
Besides this, there is a very easy-to-reach motorway connection, which enables us to reach both northern and southern Italy very quickly. The climate is really mild and agreeable, and the landscape is a mixture of hills and seaside. We must not forget the people of this part of the country; they are really reliable, serious and deep-rooted.
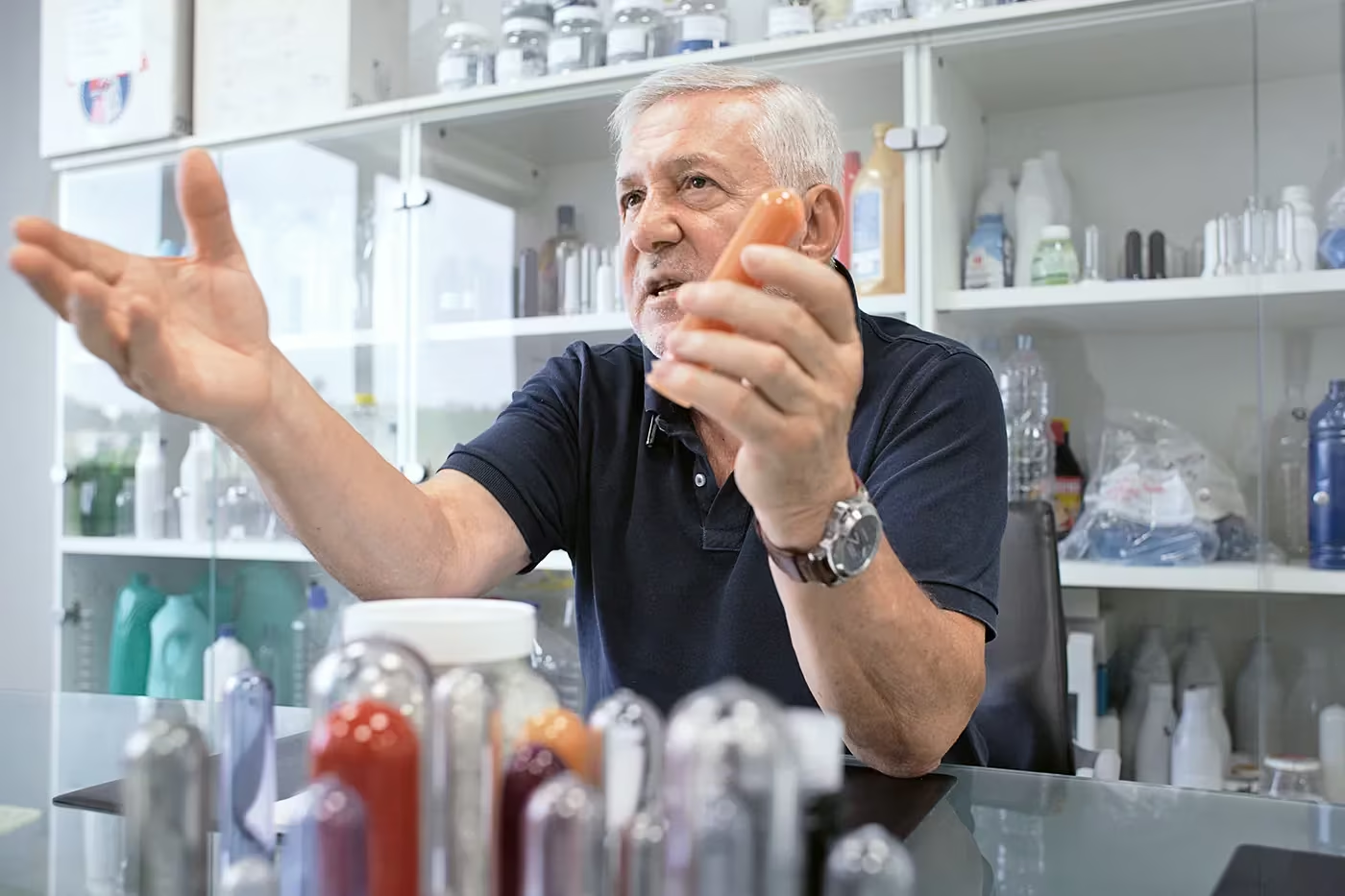
The public is increasingly critical of PET bottles. To what extent is this an issue with your customers?
It is a fact that there is a campaign against the use of plastic bottles. However, we have to be quite realistic and be aware that there is no substitute material that can provide the same advantages that PET has brought into our market.
I think it is very unrealistic to expect that we should completely eliminate plastic simply because of our inability to get people to learn how to treat it, but I do think and hope all this campaigning will be useful to help improve recycling.
What measures is Italy taking to get more used PET bottles back into the raw materials cycle?
The recycling of PET bottles is still not well organised in Italy. In spite of this, the quantity of plastic waste collected is rising steadily according to the trade association. The recycling rate is at a little over 40 per cent. The income from the fee on PET preforms, unfortunately, is not used to improve the recycling quota, but goes to the communities to finance general waste disposal. Generally speaking, however, waste management is about to further adapt to EU standards. As in other areas, a big difference exists between the provinces in the north and those in the south.
Lempa lies in a tectonically special region. How is production influenced by this fact?
Indeed, we live in a zone subject to a higher threat from earthquakes than others. The event which shook our region severely in August 2016 and caused major damage in some villages had no serious consequences for us because we strictly followed the very stringent rules on constructing buildings that can withstand earthquakes when building our premises.
The silos shook, but there was no damage to buildings or machines. The snow, however, caused us serious problems. In the winter after the earthquake, it snowed so heavily that part of the roof on our production facility collapsed. We had to put up with a production standstill of several weeks and incurred considerable costs to get the operation up and running again.
In 2004, you commissioned your first 72-imp. mould from OHAG. What prompted you to take this step?
Our speciality is to be flexible, and this goes back to the variety of moulds. The decision for or against a mould depends primarily on the type of system. Since 1998, we have been producing with a 48 cavity mould from Otto Hofstetter AG, and our experiences have been positive. In order to get more productivity, especially in the 38-millimeter market, the change was obvious.
Where do you see the strengths of the Swiss company?
Otto Hofstetter AG is also in the hands of one individual owner, who is actively engaged in the business and available to customers when necessary or desired. The employees are qualified and have the required competences to enter into agreements and enforce them. Getting in touch is quite easy for me, as I visit the Italian-speaking part of Switzerland regularly.
What does the future of Nuovaplast look like?
In January 2019, an Italian Private Equity fund acquired 75 per cent of Nuovaplast, and I have since agreed to be available for a further three years. A new general manager is going to start at the end of October.
Many thanks for the discussion, Mr Tomasoni. We wish you all the best for the future.
Nouvaplast s.r.l.
Strada Provinciale Per Sant’ Egidio, 64010 Villa Lempa, Italy, Telephone +39 0861 91 7655
- Specialised in the production of PET packaging articles
- Application areas: Mineral water, edible oil, milk, detergents, body care products and cosmetics
- Production volume: 2.5 billion preforms per year
- Infrastructure: 9 production lines