Jules Müller, why are we meeting at your chicken coop?
Breeding chickens is a hobby of mine. It’s something that has fascinated me for a long time and this is where I go to find my daily balance. I started twelve years ago. After a couple of false starts with other breeds, I finally found “my” chicken, the Orpingtons. This calm, large and robust breed has a friendly nature that suits me well. It’s a chicken that also corresponds to my visual expectations because it conforms to certain ideals of beauty. For me, breeding is not just a hobby, but also a form of relaxation.
What is your relationship generally with animals?
Since childhood, I have always had animals around me. During my younger years, I travelled a lot as I pursued my professional training. I had to put my hobby on hold. Animals are always honest and authentic and each animal has its own personality. That fascinates me. Even though I used to have other small animals, I have always been drawn to poultry. When we found the right house, I was able to fulfil my dream and breed them.
What else do you do in your free time?
I enjoy spending time with my family. We like to go skiing – and luckily many good ski areas are within easy reach of our home. Another source of pleasure for me is a good glass of red wine. The fine differences in the craft can be decisive to the quality of a wine. I’m part of a small group of colleagues who meet four times a year for an evening wine-tasting. Personally, I particularly prefer wines from the Spanish regions of Rioja and Ribera del Duero. Travelling is also something I enjoy a lot. Every year we go on several short or long trips, for example to the Palatinate region of Germany, or Vienna or the Italian-Swiss canton of Ticino. I’ve also travelled to South America, Australia and New Zealand.
What is your favourite travel destination?
I’m fascinated by other cultures, so I have to say the whole world is my favourite travel destination. I would love to travel to every country, because each one has its own special wonders. It’s important to travel with open eyes and see the beauty of the world. However, mass tourism does not appeal to me. I want to get to know the people, eat where the locals eat, and really experience the culture.
You live in Kaltbrunn, work in Uznach and grew up in Näfels, all communities that are close to each other. What does this region mean to you?
This region, which we call the Linth Plain, means home to me. My roots are here, and we have everything you could wish for: Mediterranean flair, high alpine mountains, clean lakes and rivers, and very good transportation links. With no natural resources and a lot of marshlands, this area used to be very poor. People here could only get ahead through hard work, and this gritty mentality is still noticeable today.
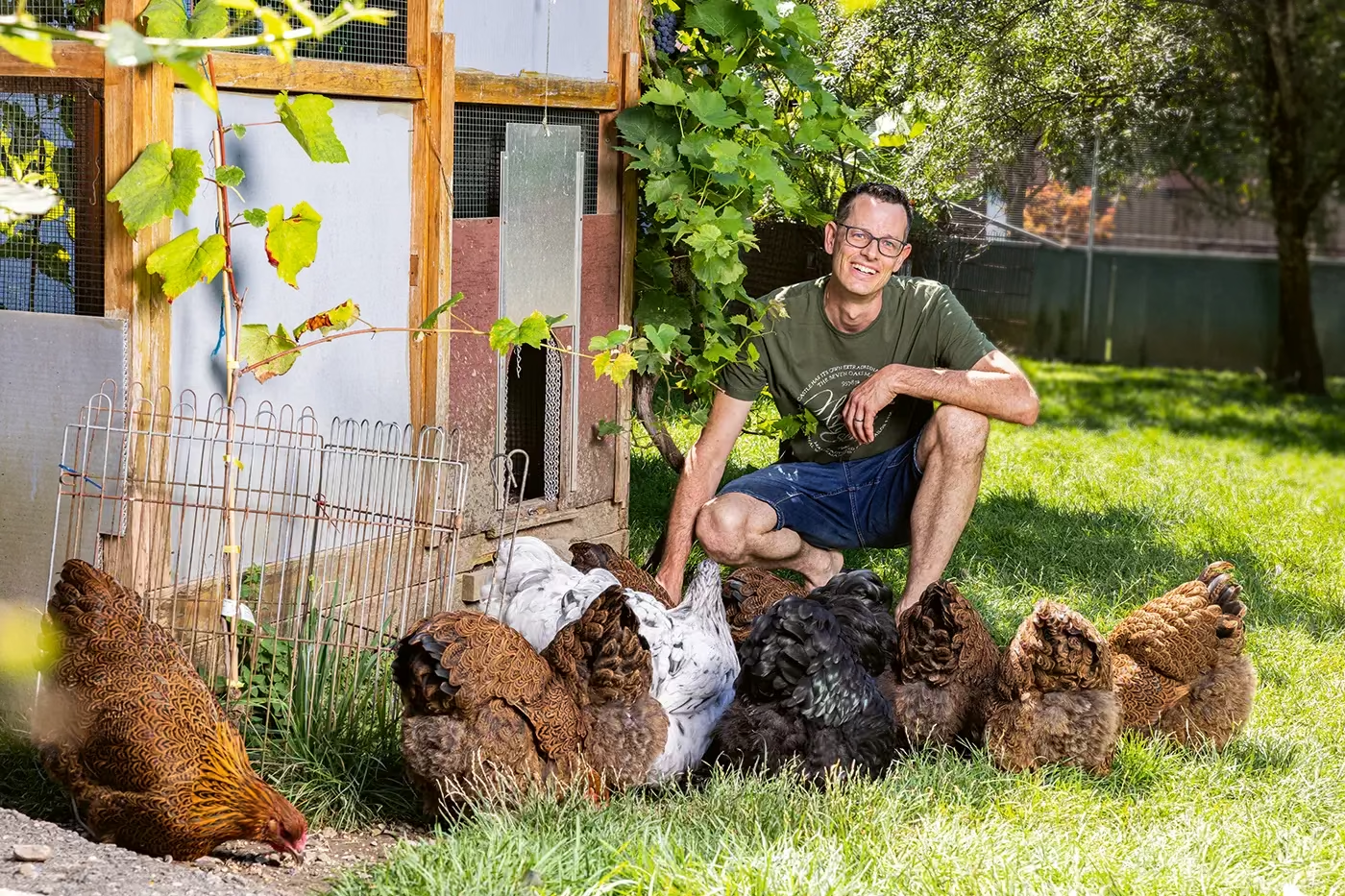
The majority of employees at Otto Hofstetter AG come from nearby. To what extent does this characteristic influence the work?
The solidarity and the willingness to go the extra mile for customers are strong characteristics that can be felt throughout all of our teams. There’s a natural spirit of togetherness that people from this region are probably born with, along with the will to overcome challenges. This makes many things possible and, I think, is a significant benefit for our customers. Our stubborn focus on problem-solving and quality may go unnoticed, but it’s second nature for us.
You are a production manager at OHAG. What are the similarities between running a chicken coop and a factory workshop?
There are certainly some parallels. Both breeding and production are about continuous improvement and the selection of suitable groups that work together harmoniously and are jointly responsible for the next generation. As with my breeding chickens, I also attach great importance to excellent training at the company for the apprentices. Both the chickens and the employees need an environment in which they feel comfortable and can develop.
How do you explain your role at OHAG to an outsider?
That’s easily summarised. As a production manager, I manage production. That sounds very simple, but there’s quite a lot to it. I see myself as a coach for my team. We are all individuals with different ambitions and needs. In addition to professional coaching, interpersonal situations are also an important part of my role. I see my responsibility as meeting the requirements of our customers in every respect together with my teams.
What does a typical working day look like for you?
My days are very varied. I usually start between 6:30 and 6:45 in the morning. My tasks include preparing for regular meetings, design meetings and deadline meetings as well as evaluating new machines and processes. But employee discussions and problem-solving are also always on my agenda. If necessary, I’m also ready to jump in and work on the production line, too. I do whatever I can to support my teams.
Moulds sold all over the world are created under your supervision. What do you know about Otto Hofstetter AG’s reputation in the industry?
In production, we rarely have direct customer contact. But we know from our colleagues and from management that our moulds enjoy an excellent reputation. Otto Hofstetter AG is well known for its durable and high-performance moulds, which many consider to be the benchmark in the industry. From my previous jobs, I can say that we also enjoy a lot of respect from our competitors. In the field of chicken farming, you would say that we are the standard-setters.
After the design and specification steps, the actual production of a mould obviously plays a major role in its final quality. How do you ensure that quality is always at the highest level?
Our engaged, motivated employees embrace the high quality standards at Otto Hofstetter AG. And team spirit is strong, which means we can achieve a lot. In addition to the modern machinery we have at our disposal, precise and seamless communication is essential to achieve the best results. And, of course, it is important for errors to be avoided or minimised right from the start.
How do you motivate your teams when additional work needs to be done?
My teams know their goals and usually organise themselves when additional work is required. If something is urgent or a bottleneck emerges, I’m there with them to support them. I think my people appreciate that. With our good communication as a group, I know I can count on everyone rowing in the same direction.
How has your role changed in the eight years as operations manager?
The technological changes in our area have been manageable in recent years. However, digitalisation and the shortage of skilled workers do pose challenges for us. We will probably have no choice but to face up to these challenges and further exploit the possibilities of modern automation and digitalisation. This will make processes more efficient while at the same time compensating for the shortage of skilled workers.
What stops have you made during your professional career?
I completed my apprenticeship with a mould maker in Näfels, Switzerland. Thereafter, I worked for another five years to complete my training as a federally certified master mechanic. This was followed by a year at Kunststoff Schwanden, five years at a precision mechanics company in Zurich and another five years at a mould maker in the Schaffhausen area. After the birth of my first son, I returned to Näfels and took on the role as production manager at Otto Hofstetter AG, before moving to Uznach five years later.
What do you think of the wave of digitalisation and automation that industry is experiencing?
Technological change is advancing rapidly today, no doubt, and it’s up to us not to miss the boat. Automation has been good for us for a long time. But, that said, with growing digitalisation it is important to weigh the benefits versus the costs. As a rule of thumb, I think keeping something as simple as possible ensures that it will be used.
What goals do you want to achieve as a plant manager in the near future?
Producing our moulds must be regarded as an attractive profession by the next generation. To do this, we have to use smart, digitally networked, easy-to-use processing machines. The upstream and downstream processes must also be continuously improved in order to continue meeting our high quality standards. This is the only way to ensure the long-term satisfaction of existing and future customers.
And privately?
My aim is to stay healthy and accompany my children into the future.
Thank you for the interview and all the best for the future.