Feedback from Otto Hofstetter AG’s customers around the world confirms just how durable and reliable the moulds from Uznach are. Customers usually report tool availability of over 97 per cent and 25 million cycles or more without an overhaul, with a mould service life of more than 25 years. Performance levels like this testify to Otto Hofstetter AG’s comprehensive engineering and manufacturing expertise.
Customer benefits in focus.
This total process know-how is the basis for the Cavity Lock technology that distinguishes the PET preform moulds of Otto Hofstetter AG. The system, developed in the 1980s by Otto Hofstetter AG’s development manager at the time, Luiz Fernandez, reduces wear and optimises the maintenance and longevity of the moulds.
More stability and less wear.
With the Swiss mould manufacturer’s Cavity Lock design, the stable mould plates take on the task of aligning the various stack inserts that shape the preform. The total surface area of the taper is around twice that of moulds from other manufacturers. The result is much more stability and much less wear. Initially, centring bushes were responsible for aligning the cores, but since 2010, this task has been done directly through a high-precision guide set in the core plate. This means that the core is positioned without coming into contact with the other stack parts. In order to achieve a long service life with low maintenance, special attention has been paid to the only dynamic separation in the OH stack. This design also has the further benefit that an additional locking ring is unnecessary. Due to its precision manufacture, the mould opens and closes with practically no friction, which in turn has an extremely positive effect on wear resistance and, thus, service life.
Holistic approach adds value.
In addition to the precision design and manufacture of its moulds, Otto Hofstetter AG has put a lot of energy into the development of highly effective coatings. The finish applied to components that are exposed to higher forces due to their position and function, and are therefore more susceptible to wear, serves to increase the durability of the moulds. As an injection mould pioneer, Otto Hofstetter AG introduced TiN coatings on the mould’s cores and neck splits as early as 1985. Since 2007, OH-Xtreme® has been the standard coating for neck splits. As the experience of operators of PET preform moulds from Otto Hofstetter AG has confirmed over the past 15 years, this exclusive coating is extremely durable, offering optimal sliding properties and assuring extremely low maintenance costs. Together with the chrome coating in the taper of the cavity, operators can achieve extraordinarily long running times. Numerous moulds have completed over 25 million shots with their original stack inserts, including the original thread splits.
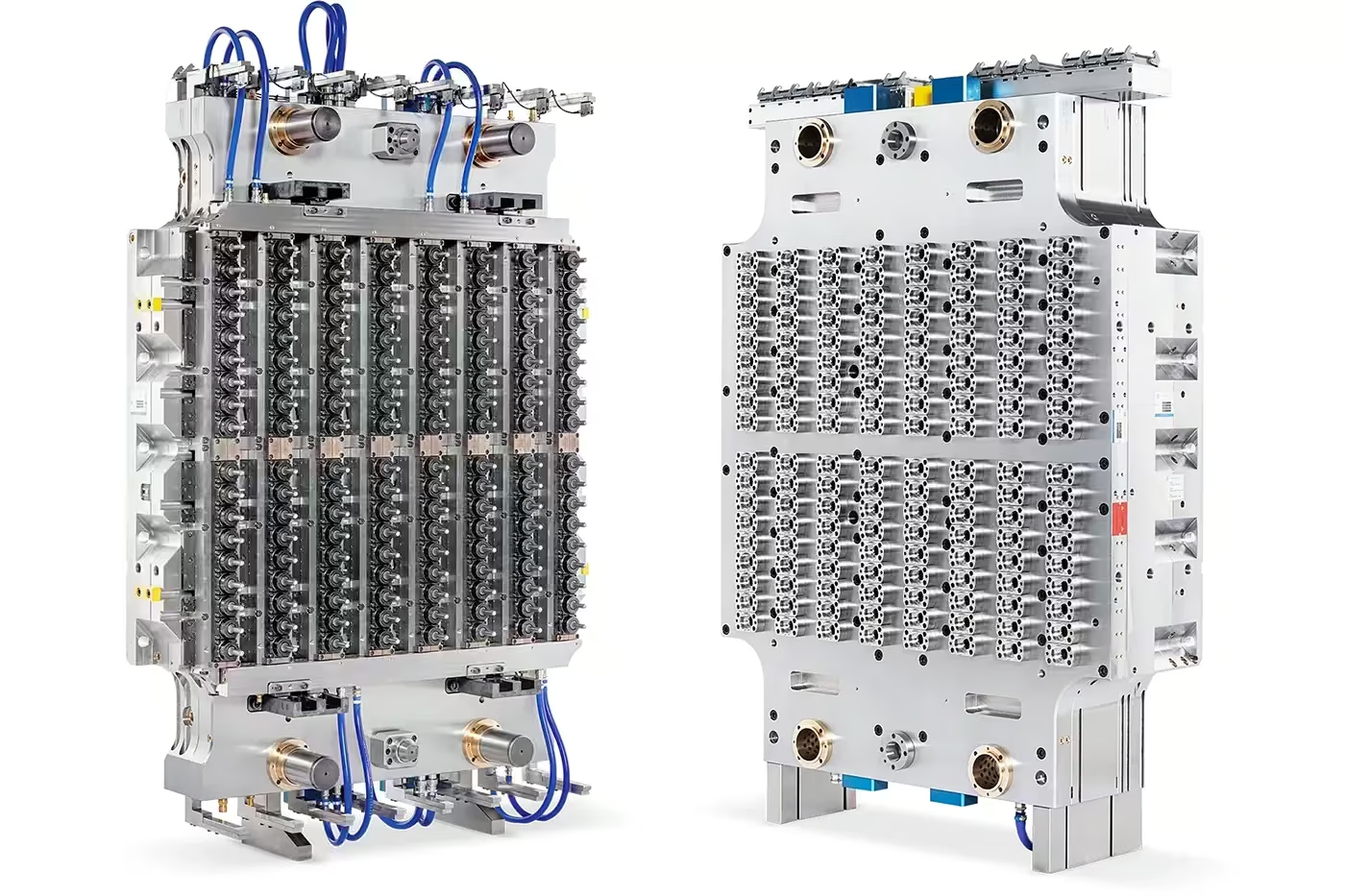
Durable and used worldwide.
Otto Hofstetter AG has not only been perfecting its exceptional Cavity Lock system in its workshops in Uznach. It also draws on the extensive experience gathered from its customers around the world in everyday production.
To date, more than 2200 Otto Hofstetter AG moulds have been delivered worldwide, totalling over 150,000 cavities. And the company continues to actively develop new ways to offer its customers moulds with even higher performance and even longer service lives.
Added tech for maximum effect.
In addition to their remarkable modularity, four additional tools increase the versatility and effectiveness of PET preform moulds from Otto Hofstetter AG. OH Xport is a smart assistant that reduces expensive production downtime and supports timely, proactive preventive maintenance. OH Xblow is an automatic cleaning system that tripples the production time with rPET in between two cleanings. Then there is the proven technology of OH-Xcool®, which reduces cycle times and accelerates the cooling process by up to 15 per cent. And finally, by dedusting the hot runner on the fly, OH-Xtract® ensures more time spent in production and less time needed for maintenance.