The prime objective of the engineers and designers of Otto Hofstetter AG is to bring the efficiency of the manufactured moulds to the maximum. This is why a utility of more than 95 per cent is not unusual in many production plants of Otto Hofstetter AG customers around the world.
Efficiency thanks to quality.
Design and function concepts optimised a thousand times over and materials of maximum robustness, coupled with the highest precision during processing, contribute very substantially to the moulds’ effectiveness. But there is more to it! Numerous in-house technical developments with which the moulds from Uznach are equipped in their standard format further increase the already high basic productivity.
Availability continuously optimised.
Take OH-Xtra®, for example. This designation stands for an entirely new concept for the surface treatment of cores. A special process applies it directly to the mould component and leads to positive effects for both mould and preform. On the one hand, fewer dust particles settle on the actual moulding surfaces, which markedly reduces the necessary cleaning effort, increasing the availability of the injection mould. On the other, tiny scratches in the gate area are prevented and, as an extra benefit, less ejection force is required.
OH-Xtreme® is another example of an invention of Otto Hofstetter AG which leads to a higher utility of the moulds. This is an amorphous metal-carbon layer which stands out through its dark colour and reduces wear to a major extent. For ten years already, the special coating has been proving its worth in daily use. It protects against seizing and fretting corrosion, and enables the dry running of moved parts such as ejectors, slides and cores.
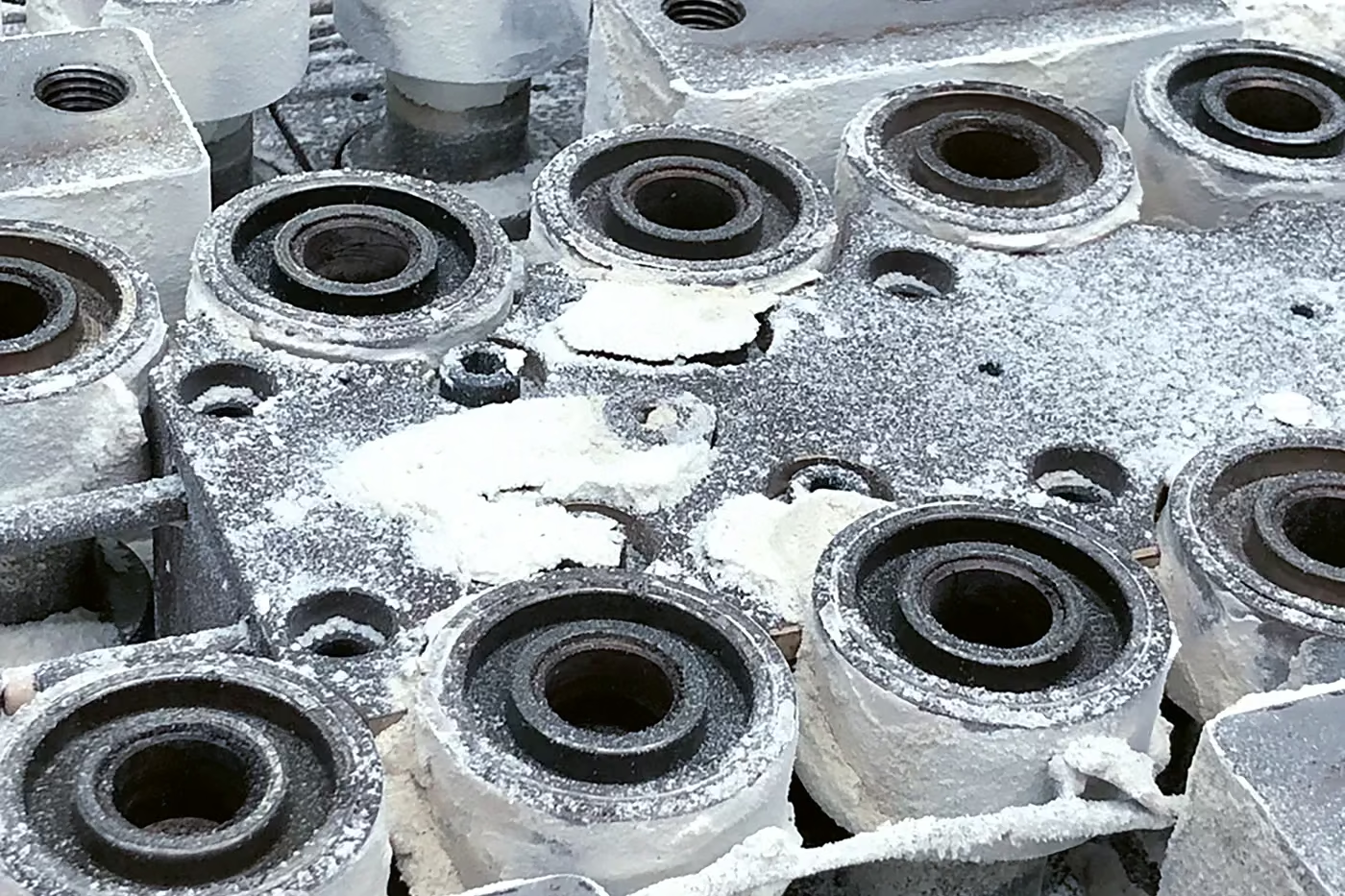
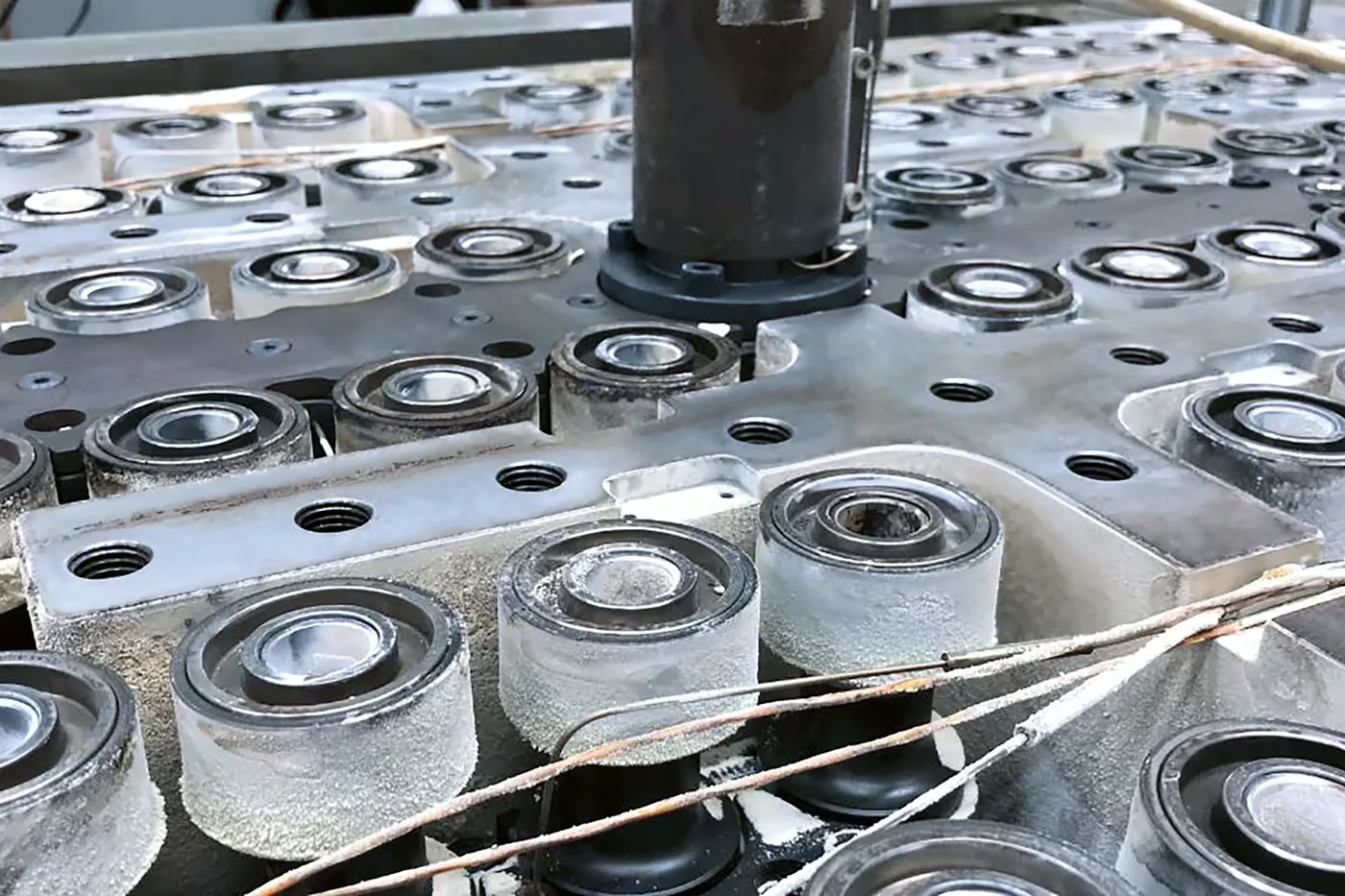
New recipe for yet more efficiency.
Only a few weeks ago, the development team of Otto Hofstetter AG launched a further new development which is available as from now: OH-Xtract® is a specific dust evacuation for moulds used in the production of PET preforms. It is integrated directly in the mould and can be adjusted individually over a timer, i.e. the feature is gentle on resources.
PET dust is everywhere.
Degassing and thereby the occurrence of PET dust is un-avoidable wherever PET is processed. This dust contaminates primarily the hot runner, but unwanted deposits also arise on the cold side of the mould, and even some parts of the moulding machine suffer from it in continuous production.
Remove the dust where it arises.
OH-Xtract® developed by the engineers of Otto Hofstetter AG acts where the dust particles are generated: in the hot runner. Thanks to extra vent bores in the head plate and an ingenious suction system, the dust can be removed or minimised before it can spread to other parts of the mould or machine. This positive effect has been substantiated impressively in comprehensive tests in production at full capacity.
Almost four times less maintenance with OH-Xtract®.
The integrated dust evacuation of Otto Hofstetter AG means that a much higher number of cycles can be performed before the equipment needs cleaning. The concrete figures show how efficiently the system works. In the test run, production only had to be interrupted for hot runner maintenance after 10 million shots. This means that OH-Xtract® allowed production to run for 144 hours longer before a production stop for maintenance was required. On a 96-cavity mould with a six-second cycle time, this would result in 8,294,400 more preforms being produced during the same period.
Impressive savings.
The new development from Uznach also allows for significant savings to be made. If you multiply the 144 hours that would be required for maintenance work by the industry standard costs of EUR 800 per hour of system downtime, the potential savings created by OH-Xtract® within the first 10 million cycles amount to EUR 115,200 – an impressive sum.