Driven by increasing demand for larger volumes of drinking water, the market for home and office delivery (HOD) is growing rapidly. At the same time, health concerns about polycarbonates are accelerating a switch to PET. Unfortunately, there have been few good options on the market that are specifically tailored to meet the production demands of large-volume PET preforms. But now, Otto Hofstetter AG and Otto Systems have joined forces to create a fully optimised production solution for this growing market segment.
Manufacturing PET preforms for the home and office delivery (HOD) market involves some difficult technical challenges. For starters, the considerable wall thicknesses and the large volume of material they employ create a risk of waves or ribs forming during the injection process. In addition, deformations such as ovality or crystallinity can also arise, which can noticeably impair the mechanical and visual integrity of the plastic and lead to problems in the subsequent stretch-and-blow moulding process. Thus, the unusual dimensions of HOD preforms require a specialised solution. Until now, the systems available for producing PET preforms for HOD containers have been at best only partially designed for this demanding application.
Moulds from the best source.
Now, PET preform manufacturers for the HOD sector have a better choice. They can use the new, fully optimised production system for HOD containers from Otto Hofstetter AG and Otto Systems.
It all starts with Otto Hofstetter AG’s new 8-cavity mould for HOD preforms, another example of the Swiss company’s comprehensive expertise in PET preforms. The mould’s exceptional cooling performance is achieved with OH-Xcool, our proprietary enhanced cooling channel that smoothly and quickly dissipates the considerable heat the process generates. In addition, the new mould’s sliding surfaces are coated with OH-Xtreme, the low-friction, no-maintenance coating that has demonstrated its advantages for years on moulds for small-volume PET preforms, assuring high quality and efficiency and a long service life. The new HOD moulds are also equipped with Otto Hofstetter’s proprietary Cavity Lock technology, which further increases the service life of the moulds while reducing maintenance.
The high-precision positioning of the stack inserts ensures virtually seamless operation. In combination with OH-Xtreme, the technology helps to ensure consistent performance over millions of cycles while at the same time significantly extending the service life of the moulds. The hot runner has also been adapted to the special requirements of HOD preforms. In order to ensure optimal yet gentle material distribution as well as ideal process conditions, the channels have been revised to optimise their flow properties.
A jewel of a mould needs the right setting.
The full potential of this new mould for HOD preforms is fully exploited in combination with the HOD-Series 160 production line engineered by Otto Systems, the sister company of Otto Hofstetter AG. The synergy between the mould and the production system delivers the efficient production of PET preforms for large-volume containers.
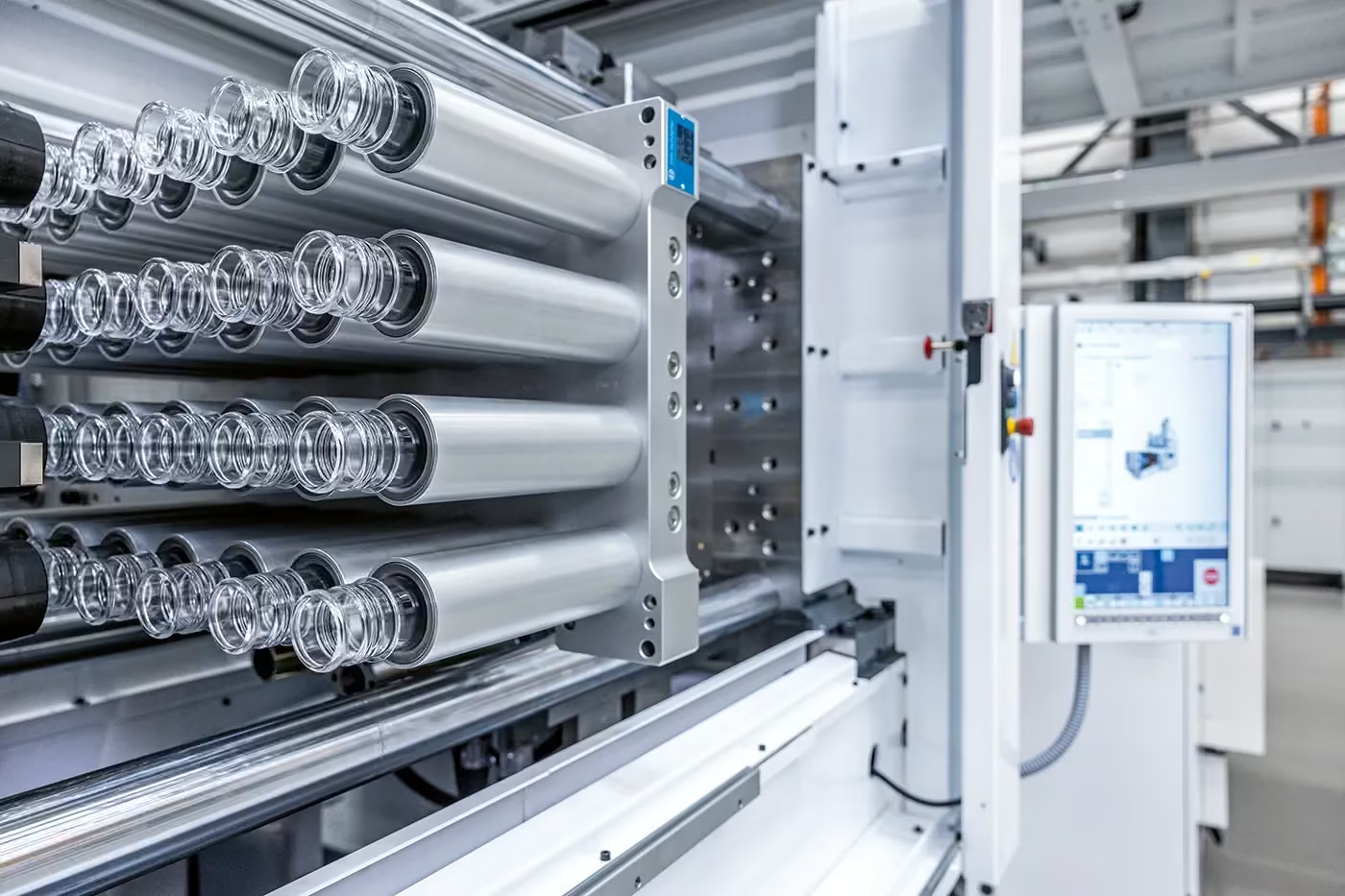
The HOD-Series 160 from Otto Systems features a range of innovative technical solutions. For example, it has a unique, outward-bending, electrically operated toggle lever mechanism that enables highly dynamic movements with minimal energy consumption. By lengthening the toggle levers, the columns and the machine bed, opening strokes of almost one metre are achieved. In addition, the high-performance plasticisation stands out, ideally balancing the plasticising and the injection processes.
Some other decisive developments in this system include the plasticising screw, which smoothly plasticises unusually high shot weights, and what is known as the Time Safe Unit (TSU). This component handles the substantial and prolonged pressure conditions required by large preforms. This means that the screw can ensure long dosing strokes with an ideal dwell time at a moderate speed. The optimised coordination of this step is vital and this extremely compact solution guarantees optimal process conditions.
Fit for special cases.
Another outstanding feature of the HOD-Series 160 from Otto Systems is the unique post-cooling arrangement with 2+2 stations. The compact design of the mould and the clever placement of the removal plate make it possible to increase the number of post-cooling cycles from two to four. The width of the removal plate was doubled to accommodate eight rows of water-cooled sleeves. Together with the Pick-Blow combi system for internal preform air cooling, optimal shaping is achieved. This concept enables faster cycle times and increases efficiency in the production of heavy and thick-walled HOD preforms.
Production efficiency.
The HOD-Series 160, equipped with the 8-cavity injection mould from Otto Hofstetter AG, offers PET manufacturers impressive technical specifications and performance. Preforms are produced for a 5-gallon disposable container (19 litres) with a snap-on mouth with a diameter of 55 millimetres.. With an inner diameter of 46 millimetres. and wall thicknesses of over 6 millimetres., the preform weighs 330 grams. The 160-ton system with 4100-TSU-100 achieves an average cycle time of 35 seconds, which is significantly faster than current offerings on the market.
Ready for an infinite variety of applications.
The combination of the 8-cavity HOD mould from Otto Hofstetter AG and the HOD-Series 160 from Otto Systems marks a significant step forward in the efficient production of large-volume PET containers. The possibilities of this power duo are very broad. Weights, necks and base geometries can be tailored and optimised to the specific application. The HOD Series concept shows how engineering expertise combined with in-depth industry knowledge can master complex challenges in today’s modern production. Applications for beer kegs or containers for agrochemicals and other technical products are also possible with this solution.