Anyone who has ever bought the famous vanilla soft ice cream from one of the globally known fast-food chains also knows the spoon that comes with the ice cream. This article developed especially for the purpose is made by injection moulding. Different producers around the world make the spoons by the billions. A suitable mould is needed for the production. A mould made, for example, by Otto Hofstetter AG.
Such a mould was recently overhauled in Uznach. The 24+24-cavity stack mould had been in operation since May 2008, and produced nothing but soft ice cream spoons on five or sometimes six days per week in a six-second cycle. The failure of some cavities and quality deficiencies in the spoons prompted the company to have the mould completely overhauled.
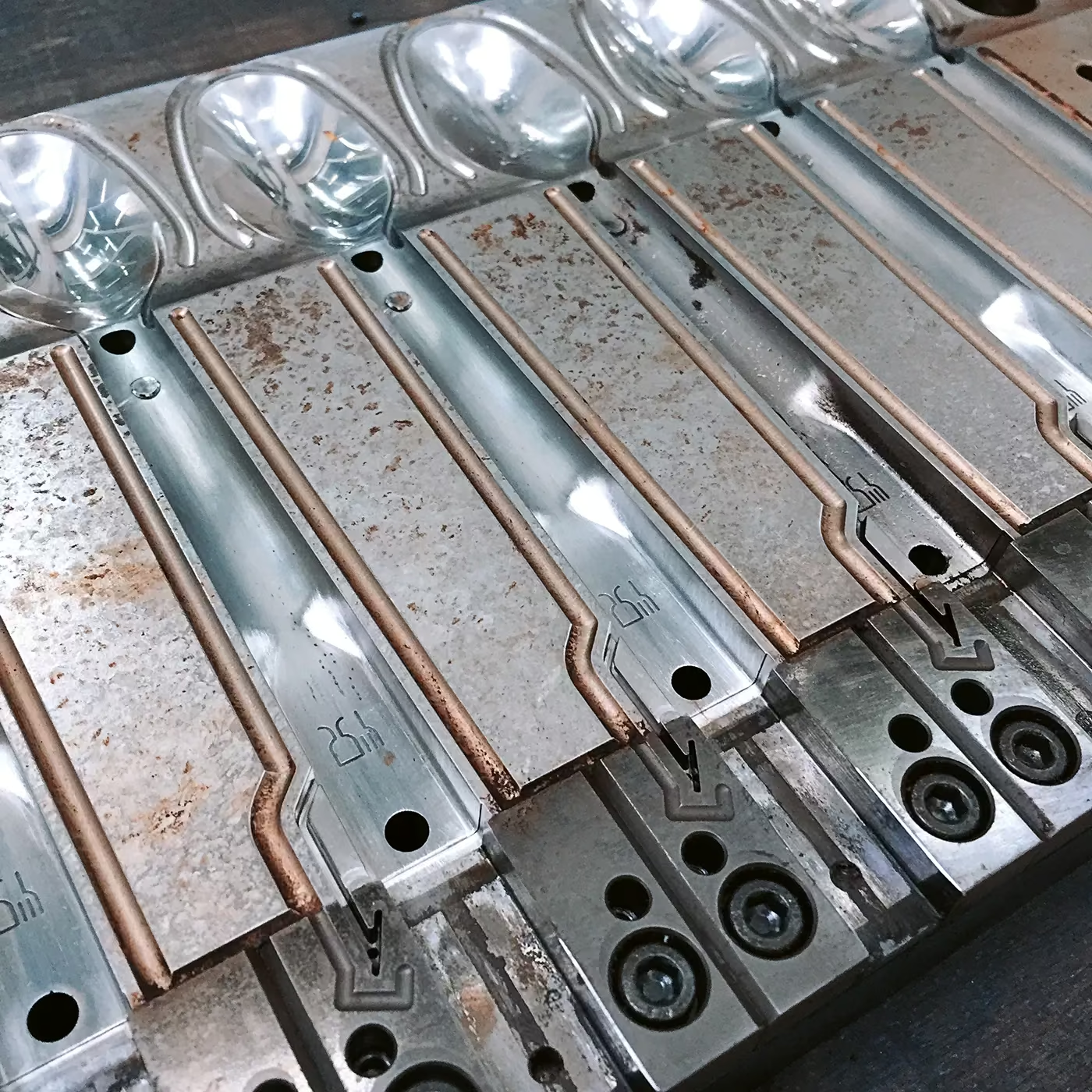
From old, make new.
Thanks to the quality of the materials used, the mature process technology and the precise execution, an injection mould from Otto Hofstetter AG can be overhauled several times. There are a number of advantages if the overhaul is done by the original manufacturer of the mould. The mould is repaired by the same experts who developed, designed and built it. The replacement parts are new or in a new condition and are of course covered by a warranty. The further use of the mould reduces its ecological footprint and the investment in the overhaul amounts to only a fraction of a new procurement.
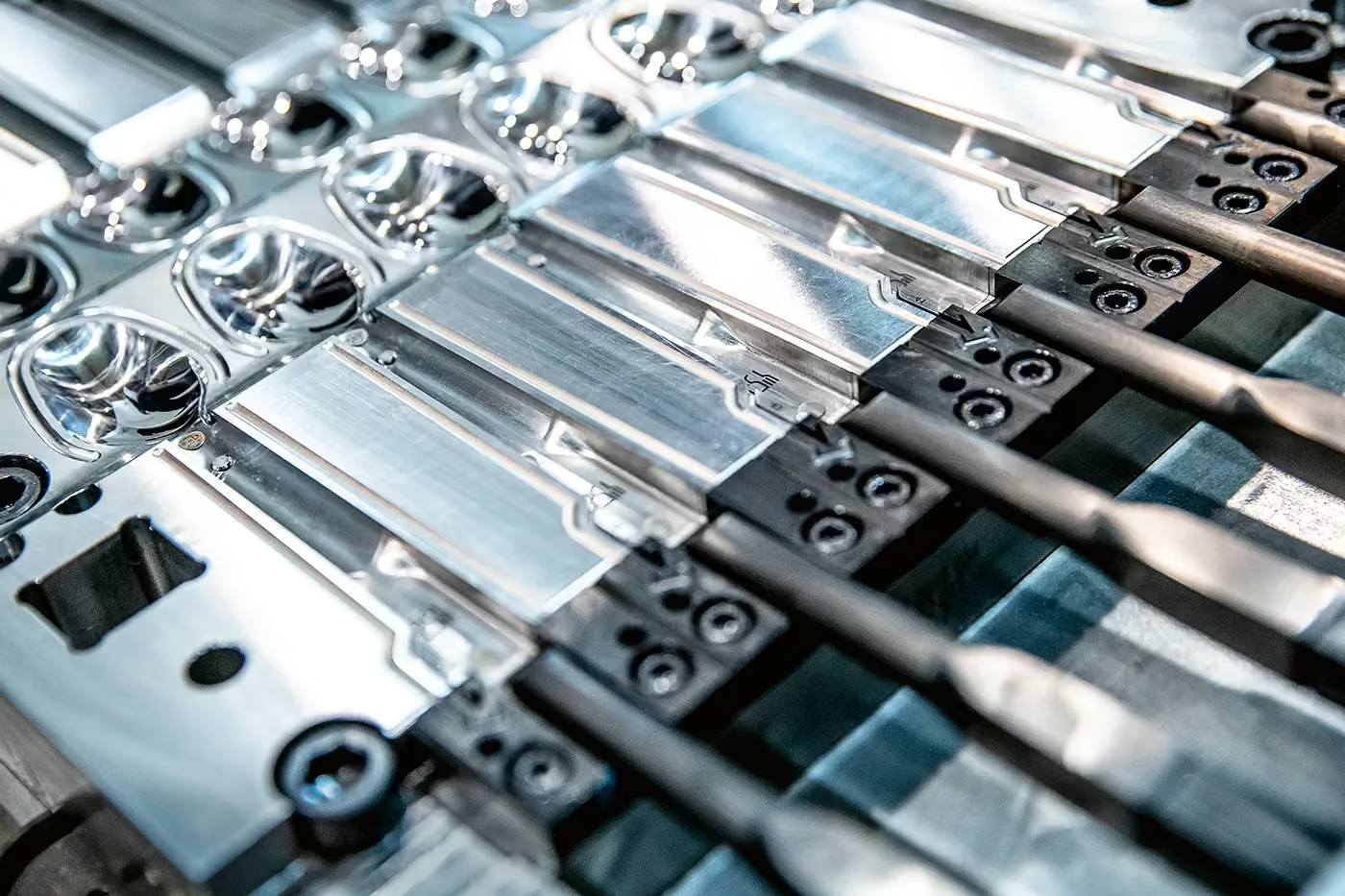
Good preparation is half the work.
The overhaul of the mould in question started with a visit to the customer’s premises. The mould was thoroughly inspected for wear and damage, and the last spoons produced were assessed and measured. Any problems during operation and mould maintenance carried out over the years were discussed with the Works Manager. This enabled the Hofstetter professionals to estimate the time required and the approximate cost of the overhaul. Conclusion: The entire group of inserts and the rack housing had to be replaced. The hotrunner and the remaining parts of the cold side needed comprehensive revision. The total time required was estimated to be 20 weeks, but the mould would be out of production for only half of this period.
Taking advantage of new developments.
Otto Hofstetter AG prepared for the overhaul while the stack mould was still producing flat out. Apart from the ordered quantity of spoons, the customer also moulded the quantity required during the weeks of the overhaul. In Uznach, the original drawings of the 24+24-cavity stack mould were retrieved from the archives and the manufacture of the replacement parts was started. In the 10 years that the mould had served its purpose at the customer’s works, the engineers in Uznach had developed the technology further and gained in-depth experience from numerous projects around the globe. The newly made mould components, therefore, were state-of-the-art technology. Part after part was pre-machined and waiting to be fitted.
Fit for the future.
The customer transported the mould to the factory in Uznach, where it was opened. The Hofstetter experts now checked the mould condition in detail. The accuracy of the initial assessment in the customer’s production usually corresponds to the effective picture in the mould manufacturer’s revision department. The deviations amount to a maximum of plus/minus 10 per cent of the initially estimated values. The experience values were also confirmed in this case. The pre-machined replacement parts were fitted and the other mould components reground and neatly cleaned. At the end of the overhaul, there was hardly any evidence of the fact that the mould had run for more than 10 years and performed well over 20 million cycles.
The spoon mould was then carefully checked and measured. As usual at Otto Hofstetter AG, no deviations from the set values are accepted. Adjustments are made until all settings comply. This is followed by initial internal sampling. The technicians in Uznach will only receive the customer in their test centre when the product (spoon) meets the specification 100 per cent. Cycling under production conditions is then carried out and the outcome checked. The result was an impeccable soft ice cream spoon: no flashes, no voids. Nothing that would not have complied with a perfect product.
The 24+24-cavity stack mould was correctly packed and returned to its proper destination in production. Thanks to a professional assessment and joint planning by the customer and the mould-maker, the overhaul was completed successfully within the agreed time.
To postpone is uneconomical.
Experience gained from many projects makes it clear that it is unprofitable to delay a necessary overhaul. Wear of individual mould components can cause consequential damage, the repair of which is likely to cost at least the amount supposedlysaved with the postponement. The enormous forces acting on the mould compress the steel. The vents in the mould section, which are sometimes only fifteen-thousandth of a millimetre wide, can shut and thereby impair correct functioning of the mould. Waiting too long, moreover, affects the mould’s economic efficiency. If cavities are lost, the quantity of produced articles decreases, the quality of the product comes down and the number of rejects goes up. It is like with a visit to the dentist: the longer one waits, the longer the inevitable treatment and the higher the cost.
Conversion for a second use.
The moulds of Otto Hofstetter AG are built for an eternity. Subject to proper maintenance and regular overhauls, their durability is usually longer than the life cycle of the packaging products moulded by them. If minor modifications of the product are required, it often pays to ask the specialists in Uznach whether a modification of the actual moulding surfaces would be a possibility and sensible, seeing that an overhauled or converted mould corresponds to a new one in every respect.