Capsul’in Pro was founded in 2010. What does the company look like today?
Rafael Mira: Capsul’in is a young company and has a very special business model. It focuses exclusively on product development for coffee capsules and controls the entire process until the product is delivered to the customer. But we don’t have our own production. We have been working with suppliers since the beginning. This allows Capsul’in to be very flexible and to adapt quickly to changing market preferences. We currently have a production partner in Spain, one in Luxembourg and one in Switzerland. Together, we achieve a total production of around 3 billion capsules. The headquarters are in Luxembourg; we also have an office in Paris and operate a quality assurance department.
Capsul’in specialises in the production of Nespresso-compatible coffee capsules. What gave the impetus for this?
Our company was founded by Laurent Lombart, Olivier Brivois and Christian Berti. The trigger was a magazine article about coffee capsules that Laurent came across during a trip. Olivier was mentioned in the article. He was working as a barista in the coffee industry at the time. Laurent contacted him spontaneously and, because they were both convinced of the potential of this business area, they began to draw up a business plan.
It appears their assessment was correct. Which markets do you currently serve?
The first customers were in France because Olivier lived there and was already in contact with them over coffee-related business. Today, we deliver to 72 countries, including Australia, Korea, Russia, South Africa, all European countries, South America, Brazil and Argentina. In other words, wherever there is a Nespresso-compatible market, Capsul’in is present.
Why do customers choose your products?
We produce and sell empty coffee capsules, but our standards go far beyond that. Thanks to Olivier Brivois’ history as a barista, we attach great importance to the quality of the coffee in the cup in all of our developments. He really knows coffee, its aroma and what goes into making the best possible coffee. And as head of R&D, he doesn’t primarily think about how to develop a capsule, but rather he focuses on the end result – how to improve the coffee in the cup. For him, the capsule is not the focus, but rather the end of the process. I believe therein lies part of the answer to your question. In addition, we also pay close attention to the quality of our internal processes for ordering and delivery.
You produce in Luxembourg, France, Spain and Switzerland, and you guarantee your customers the highest quality. How do you ensure that?
Just as we rely on the injection moulds from Otto Hofstetter AG, we also count on partners in the production of the capsules who generally also aim for the highest level of quality. In addition, our three partners control all processes according to a jointly defined formula that is based on our research and experience. In this way, quality management is an open book for everyone and not a black box.
How important is quality in a coffee capsule?
Producing a single high-quality capsule is not particularly difficult. But when it comes to producing billions of capsules that maintain uniform high quality, things do become challenging. The capsules must function perfectly both during processing and filling in the coffee roasting plant and later in the coffee machine for the end user. A product can only be successful if it meets the demands of both the coffee producer and the end user.
You use injection moulding technology to produce your capsules. What part of the quality do the moulds play?
The injection mould is the key to quality. A simple rule applies: it takes a high-quality mould to create a perfect product. We work 24 hours a day at all three production sites. That’s why we rely on moulds that are outstanding in terms of dimensional stability, durability and performance. We don’t allow any weak links in our production processes.
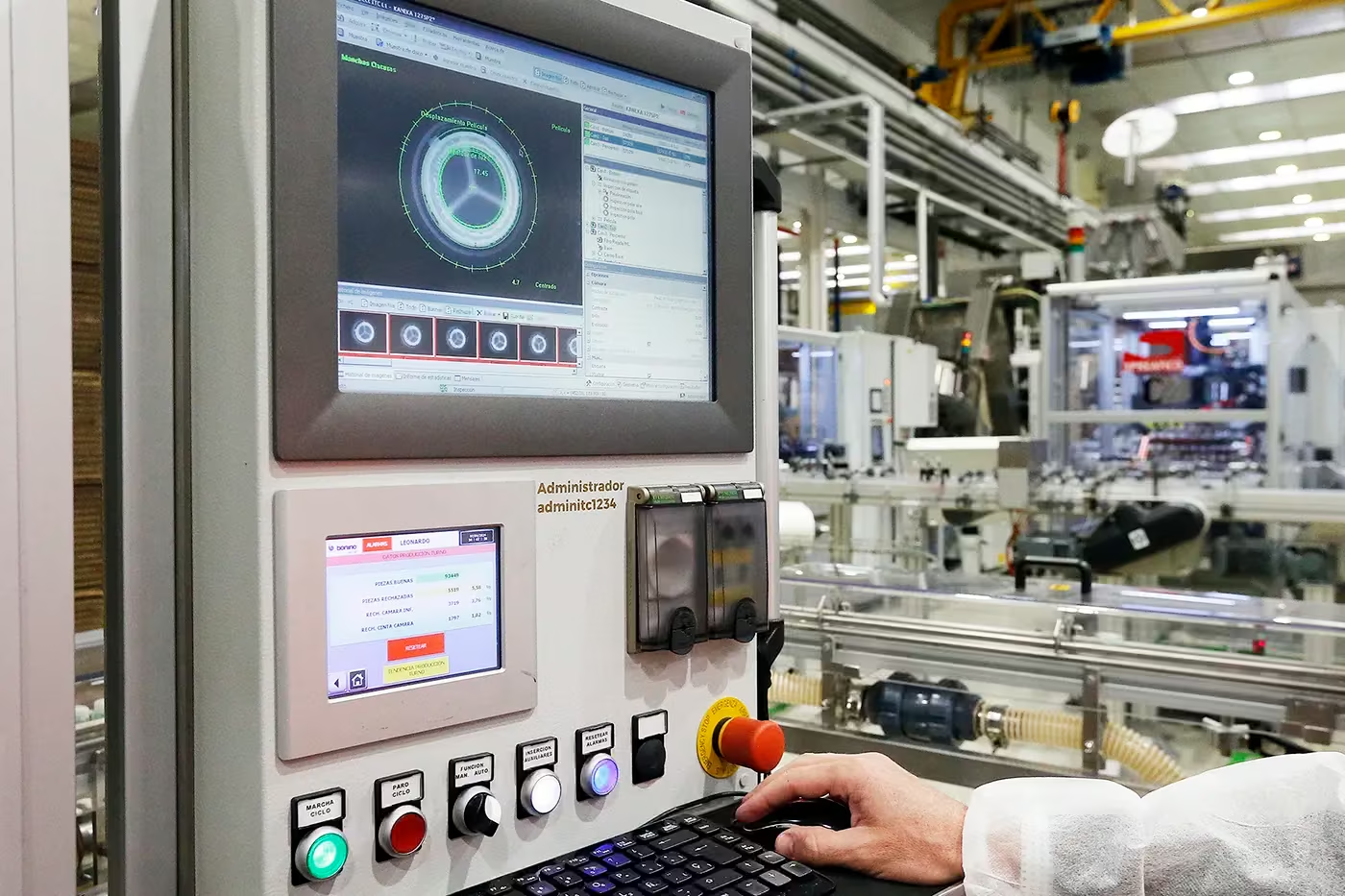
Capsul’in relies on moulds from Otto Hofstetter AG. To what extent do they meet your requirements?
The first injection mould that we bought from Otto Hofstetter AG in 2016 has been running around the clock for eight years. The 48-cavity mould achieves availability of well over 90 per cent and creates a cycle time of 5.2 seconds. We now operate eight moulds from your factory in Uznach. I already knew Otto Hofstetter AG before I got involved with Capsul’in and was aware of the reliability, longevity and the ease of maintenance of their moulds.
Where do you see potential for further optimisation?
These moulds are very complex in their construction. There are probably not many toolmakers who are able to produce them with a level of precision comparable to what Otto Hofstetter AG delivers. In addition, they are reliable, stable and durable. That’s why we work with them. In my opinion, the tools are almost perfect. Although I am aware of the dependencies between material procurement and machine capacity, I sometimes wish there were a little more flexibility in delivery times.
To what extent would an expansion of the cavities be interesting?
This would be quite realistic with conventional plastics. However, recent developments in the market are moving towards biopolymers. With these new materials, the level of difficulty in processing, on a scale of ten, increases from two to nine. This would mean that the mould design would have to be completely redeveloped. However, since we only have two to three years of experience with biopolymers, it is not yet possible to determine exactly what needs to be changed.
Like Capsul’in, Otto Hofstetter also puts their customers first. How is this reflected in your collaboration?
The team at Otto Hofstetter AG consists of very experienced specialists who have been working for the company for many years. They know our business and our moulds very well. In the rare cases where we need assistance, they respond promptly, professionally and in a customer-focused manner. In this respect, too, we have a first-class partner in the team from Uznach.
You have set yourself the goal of contributing to the growth of your customers through constant innovation. How is this achieved?
Unlike other players in our market, at Capsul’in we focus entirely on coffee capsules and do not offer other products. This focus gives us the freedom we need to monitor developments in the market and react quickly to trends and changes in direction in our business. I think we manage that quite well. For example, in 2015 we were the first supplier to produce capsules from a biodegradable material from BASF using the injection moulding process.
This focus on capsules comes with a certain entrepreneurial risk, no? How do you deal with that?
Coffee is popular all over the world. Consumption is increasing in various countries, and more countries will adopt the tradition of drinking coffee. With the increasing popularity of coffee, the market for coffee capsules is also growing. Of course, coffee in capsules requires a certain level of wealth and is more expensive than traditionally brewed coffee. But where economic power and quality of life are increasing, the trend towards coffee in capsules is also increasing. We therefore expect steady growth worldwide.
I keep hearing that the moulds from Otto Hofstetter AG are expensive. How do you see that?
The bottom line, in my opinion, is that an expensive mould makes the end product cheaper. Although the initial investment costs may be higher, in the end the additional costs pay off for us. Basically, we invest in high quality to avoid customer complaints. The amount of the basic investment is a question of balance.
In 2021, Capsul’in launched the world’s first 100 per cent bio-based capsule. How did the market react?
The new development received a very positive response from the market. While the capsule introduced in 2015 consisted of a mixture of fossil and biodegradable raw materials and could only be industrially composted, today’s 100 per cent bio-based capsules can be broken down naturally in domestic compost. From a business perspective, this was a very good decision.
It sounds like there’s a catch. What does it consist of?
As I said, biopolymers behave completely differently to standard materials when processed. Injection performance, cycle time and other parameters must be redefined. And since we are pioneers in this field, we could not rely on other companies’ experiences with this technology. We had to find our own solutions. After working intensively with home-compostable biopolymers since 2020, we have been able to achieve the quality we demand and can assure that quality for mass production.
Will capsules made from 100 per cent biopolymers soon replace aluminium capsules?
Today, the proportion of aluminium capsules is between 60 and 70 per cent. In my opinion, this proportion will not change so quickly. Coffee is a very demanding filling material and needs the best possible protection in order to guarantee a perfect-tasting result in the cup. Capsules made from biopolymers will probably never achieve the same oxygen and humidity barrier as capsules made from aluminium. At Capsul’in we have been working on compostable capsules for years to better protect aroma and moisture. With the next generation, we hope to replace thermoformed capsules on the market. However, aluminium remains the perfect packaging for coffee.
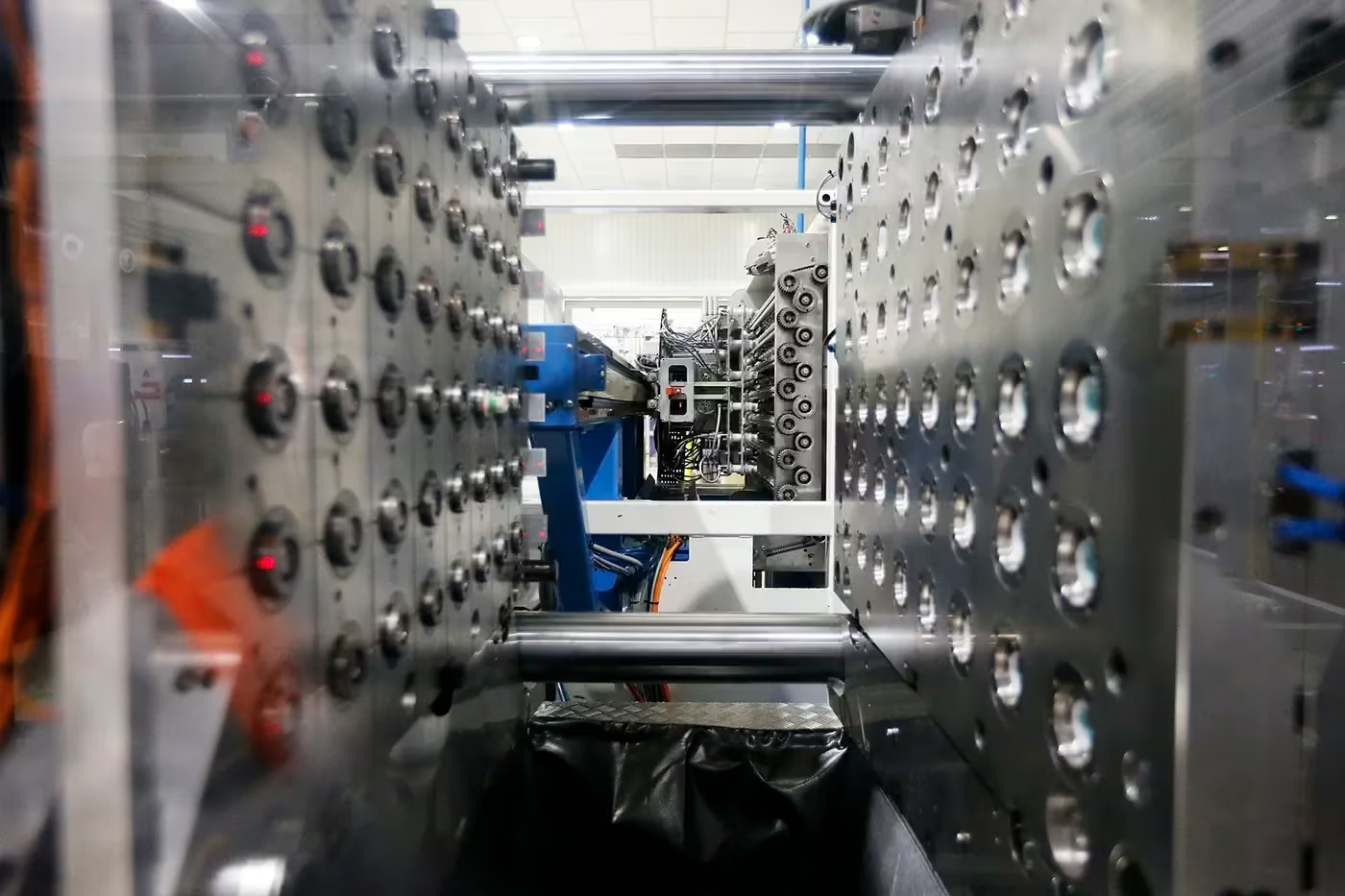
It seems to me that the development work for this solution is quite time-consuming and expensive. What motivates Capsul’in to do this?
If we hadn’t continued to evolve over the last thirteen years, we probably wouldn’t be where we are today – or perhaps we wouldn’t exist at all. Acquiring more coffee producers and opening up new markets is now only possible through innovation. We live by the principle that what we do today, we may not do tomorrow. What is made from aluminium, polypropylene or biopolymers today can be made from something completely different in just a few months. If you listen to the market, paper could be an alternative for the future. That’s why we’ve been working intensively on paper capsules since last year. We have to familiarise ourselves with completely unknown material again.
What about sustainability at Capsul’in?
As mentioned, our mission is to bring the highest taste experience into the consumer’s coffee cup. Coffee is a natural product and needs an intact environment so that a sufficient amount of aroma is present. So we have a vital interest in making our contribution to this. With aluminium and plastic, we use two materials that are controversial today. That’s why we’ve been investing in the development of alternatives since Capsul’in was founded. Our metal capsules are now made from recycled aluminium and we are gradually replacing plastic capsules with our biodegradable ones.
What kind of support do you hope to receive from your mould partner on this journey?
Today, bio-based materials in injection moulding still give us a bit of a headache. The injection moulding process is significantly more demanding and the tolerances in the process are significantly tighter than we are used to with conventional granules. In this regard, we are eager to work with the engineers at Otto Hofstetter AG to find solutions so that we can achieve flexibility with biopolymers comparable to what we have with plastics today.
What’s in the future for Capsul’in?
Given the rapidly changing market, our CEO, Laurent Lombart, raised the question of the company’s future three months ago. It’s difficult to predict where the company will be in the next five years. In any case, we want to continue to grow with our customers, and we deeply regret it if a customer chooses another partner. Our goal in five years is to be a preferred partner for various coffee systems, no longer exclusively for Nespresso. We intend to expand our expertise to other systems and are already working on technology-independent solutions. We are examining various expansion options into different systems and are open to new materials such as silicone. Maybe Otto Hofstetter AG can support us in this. The focus of our strategy continues to be to closely monitor market developments and the needs of our customers. The development of paper capsules is in full swing, and we hope to be able to offer our own high-quality paper capsules next year.
Mr Mira, thank you very much for this insightful conversation. I wish you and Capsul’in all the best for the future.